过程控制与优化
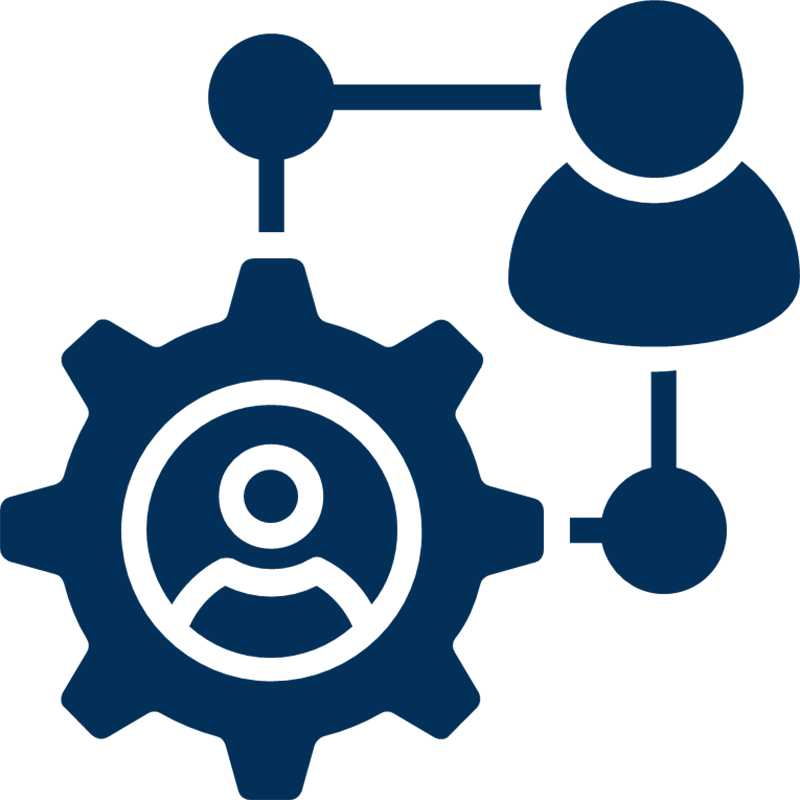
概述
过程控制和优化 (PCO) 是在不违反过程约束的情况下调整过程以维持或优化一组指定参数的学科。 PCO 市场受到对节能生产流程、安全和安保问题的需求不断增长以及能够可靠预测流程偏差的物联网系统开发的推动。从根本上说,可以调整三个参数以影响最佳性能。 - 设备优化:第一步是通过检查运行数据以识别设备瓶颈来验证现有设备是否被充分利用。 - 操作程序:操作程序可能因人而异或因班次而异。工厂的自动化可以提供很大帮助。但是,如果操作员控制并手动运行工厂,自动化将无济于事。 - 控制优化:在典型的加工厂,例如化工厂或炼油厂,有数百甚至数千个控制回路。每个控制回路负责控制过程的一部分,例如保持温度、液位或流量。如果控制回路没有正确设计和调整,则过程会低于其最佳值。该过程的操作成本将更高,并且设备会过早磨损。为了使每个控制回路以最佳方式运行,识别传感器、阀门和调整问题很重要。已充分证明超过 35% 的控制回路通常存在问题。持续监控和优化整个工厂的过程有时称为绩效监督。
适用行业
- 运输
- 设备与机械
- 化学品
适用功能
- 离散制造
- 质量保证
市场规模
案例研究.

Case Study
Ensures Tanker Safety and Emissions Compliance
Storage tanks are irregular in shape and a certain amount of mathematical modelling is required to get an accurate representation of volume and, more importantly, the weight of material in each tank. In addition, countries have different emission regulations, so the ships position needed to be accurately known in order to geotag emission data.
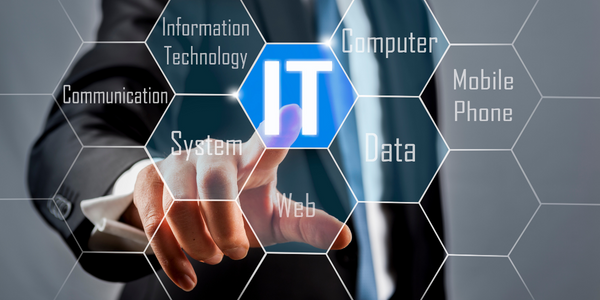
Case Study
Consolidating the IT landscape
The IT architecture had grown over 15 years and the EDI communication was spread across several EDI server. This involved high efforts which were to be reduced with the introduction of an EAI standard software:- Connection of about 100 partners and 400 customers, exchange of highly heterogeneous message formats, i.e. record structures, EDIFACT, customer specific formats, XML and binary files- Connection to FTP, E-Mail, mailboxes (IBM, Eurolog, Telecom) and MQ-Series- Reduction of maintenance and evaluation efforts, easy tracing of data flows, increase in performance, introduction of central error handling
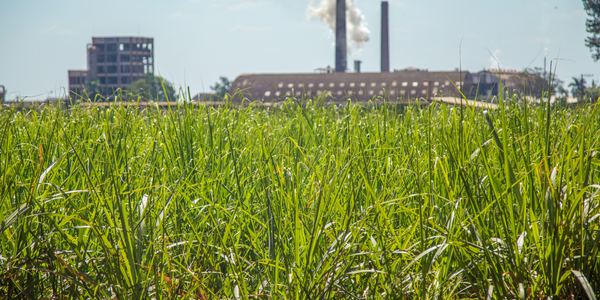
Case Study
Managing and Mitigating Risk
Czarnikow is wholly reliant upon business information management to support its global operations. The combination of manual and unstructured office based processes lacked the control, clarity, efficiency, security and governance required within the business.Information flow across the business and its counter-parties was handled through custom spread sheets, email (both user mailboxes and Microsoft Exchange public folders), Word documents and specific business function systems such as Infor SunSystems FMS for accounting and Allegro for trading/shipping. A lack of flexible and compliant process management in trade registration, credit risk and counterparty on-boarding was leading to unacceptable levels of risk in day-to-day operations. This was increasingly threatening operational capability and failing to support the strategic growth plans of the business. The business issues included:• Too many manual, cumbersome processes with inconsistent hand-offs and duplication of data entry • Pre execution enforcement of internal compliance procedures, ensuring adherence to external regulations with improved reporting and transparency • Manual processes and retrospective visibility were leading to unacceptable levels of operational risk • Inability to delegate authority across the business due to insufficient auditability and control • Limited visibility and accessibility of real-time, accurate management information to inform business decisions • Lack of global standards in compliance processing