Customer Company Size
Large Corporate
Region
- America
Country
- United States
Product
- Anypoint Platform
- Salesforce
- Clarizen
- GoFormz
- MS Dynamics AX
Tech Stack
- Cloud Infrastructure
- Hybrid Integration Platform
- API Strategy
Implementation Scale
- Enterprise-wide Deployment
Impact Metrics
- Productivity Improvements
- Customer Satisfaction
Technology Category
- Platform as a Service (PaaS) - Connectivity Platforms
- Application Infrastructure & Middleware - API Integration & Management
- Infrastructure as a Service (IaaS) - Hybrid Cloud
Applicable Industries
- Construction & Infrastructure
Services
- System Integration
- Cloud Planning, Design & Implementation Services
About The Customer
Oldcastle Precast is the leading manufacturer of precast concrete, polymer concrete, and plastic products in the United States. With more than 80 locations nationwide, their products are always close at hand. Oldcastle works with contractors and local building firms to deliver on their projects in a timely basis. The company’s goal is to provide a one-stop shop for building materials ranging from roofing and siding, all the way to asphalt and concrete. Specifically, their project management business unit works on client projects using their 1,200 local companies that are part of their network of operations to execute. Oldcastle distributes materials to the client location and a timely project delivery ensures maximum revenue and client satisfaction. In the past few years, Oldcastle has grown largely through acquisitions of various materials, distribution, and project management firms. While the acquisition activity expanded their reach and audience, it also led to a lack of systems consolidation that negatively impacted customer satisfaction. To increase the quality of customer service and ensure their place as the leading manufacturer for the next 10 years, Oldcastle had to standardize on technology across the company to streamline operations and set the company up for future success.
The Challenge
Oldcastle Precast, a leading manufacturer of precast concrete, polymer concrete, and plastic products in the United States, faced a significant challenge due to its rapid growth through acquisitions. While these acquisitions expanded the company's reach and audience, they also led to a lack of systems consolidation, negatively impacting customer satisfaction. The company had been using manual, custom-coded point-to-point integration to connect CRM tools such as Salesforce and MS Dynamics AX and project management tools like Clarizen, Box, Piece Tracker, and GoFormz. However, this approach was not scalable or cost-effective. As Oldcastle continued to expand, the lack of a centralized, scalable, and repeatable integration solution made it increasingly challenging to integrate the acquired on-premises systems and data into the central cloud infrastructure. The company needed a hybrid integration platform to meet the full spectrum of their needs.
The Solution
Oldcastle selected MuleSoft's Anypoint Platform to integrate all aspects of their new infrastructure and drive greater enterprise agility. The hybrid integration capabilities and long-term vision led Oldcastle to select Anypoint Platform, which can run both in the cloud and on-premises. The first project with MuleSoft was creating a project automation platform to allow project managers to track projects from creation of sale throughout the lifecycle and completion of the project. Oldcastle chose Salesforce as the single source of client data and began integrating Salesforce and Clarizen. Once Salesforce and Clarizen were integrated, project managers could log in to Clarizen, and view all client and project details in one location, ensuring all projects were delivered on time and under budget. The second project they chose to tackle was integrating GoFormz with Salesforce. Now that the two applications are fully connected, the problem report is pulled directly into the client's Salesforce account and the project manager can resolve any problems immediately, ensuring that equipment issues don't affect the project timeline.
Operational Impact
Quantitative Benefit
Case Study missing?
Start adding your own!
Register with your work email and create a new case study profile for your business.
Related Case Studies.
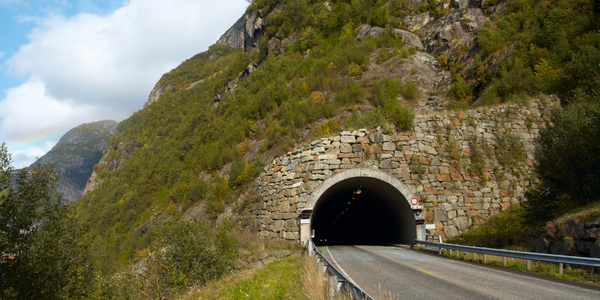
Case Study
IoT System for Tunnel Construction
The Zenitaka Corporation ('Zenitaka') has two major business areas: its architectural business focuses on structures such as government buildings, office buildings, and commercial facilities, while its civil engineering business is targeted at structures such as tunnels, bridges and dams. Within these areas, there presented two issues that have always persisted in regard to the construction of mountain tunnels. These issues are 'improving safety" and "reducing energy consumption". Mountain tunnels construction requires a massive amount of electricity. This is because there are many kinds of electrical equipment being used day and night, including construction machinery, construction lighting, and ventilating fan. Despite this, the amount of power consumption is generally not tightly managed. In many cases, the exact amount of power consumption is only ascertained when the bill from the power company becomes available. Sometimes, corporations install demand-monitoring equipment to help curb the maximum power demanded. However, even in these cases, the devices only allow the total volume of power consumption to be ascertained, or they may issue warnings to prevent the contracted volume of power from being exceeded. In order to tackle the issue of reducing power consumption, it was first necessary to obtain an accurate breakdown of how much power was being used in each particular area. In other words, we needed to be able to visualize the amount of power being consumed. Safety, was also not being managed very rigorously. Even now, tunnel construction sites often use a 'name label' system for managing entry into the work site. Specifically, red labels with white reverse sides that bear the workers' names on both sides are displayed at the tunnel work site entrance. The workers themselves then flip the name label to the appropriate side when entering or exiting from the work site to indicate whether or not they are working inside the tunnel at any given time. If a worker forgets to flip his or her name label when entering or exiting from the tunnel, management cannot be performed effectively. In order to tackle the challenges mentioned above, Zenitaka decided to build a system that could improve the safety of tunnel construction as well as reduce the amount of power consumed. In other words, this new system would facilitate a clear picture of which workers were working in each location at the mountain tunnel construction site, as well as which processes were being carried out at those respective locations at any given time. The system would maintain the safety of all workers while also carefully controlling the electrical equipment to reduce unnecessary power consumption. Having decided on the concept, our next concern was whether there existed any kind of robust hardware that would not break down at the construction work site, that could move freely in response to changes in the working environment, and that could accurately detect workers and vehicles using radio frequency identification (RFID). Given that this system would involve many components that were new to Zenitaka, we decided to enlist the cooperation of E.I.Sol Co., Ltd. ('E.I.Sol') as our joint development partner, as they had provided us with a highly practical proposal.
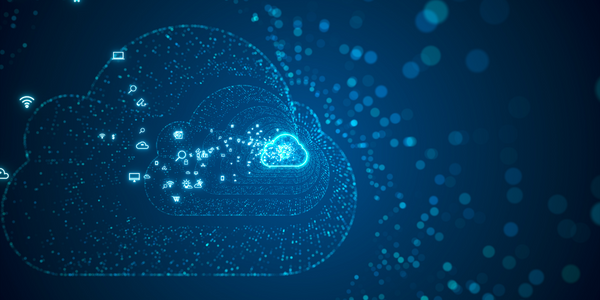
Case Study
Splunk Partnership Ties Together Big Data & IoT Services
Splunk was faced with the need to meet emerging customer demands for interfacing IoT projects to its suite of services. The company required an IoT partner that would be able to easily and quickly integrate with its Splunk Enterprise platform, rather than allocating development resources and time to building out an IoT interface and application platform.
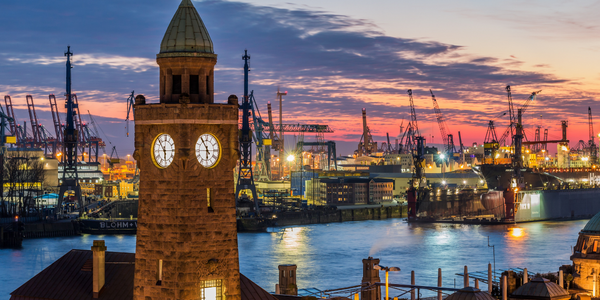
Case Study
Bridge monitoring in Hamburg Port
Kattwyk Bridge is used for both rail and road transport, and it has played an important role in the Port of Hamburg since 1973. However, the increasing pressure from traffic requires a monitoring solution. The goal of the project is to assess in real-time the bridge's status and dynamic responses to traffic and lift processes.
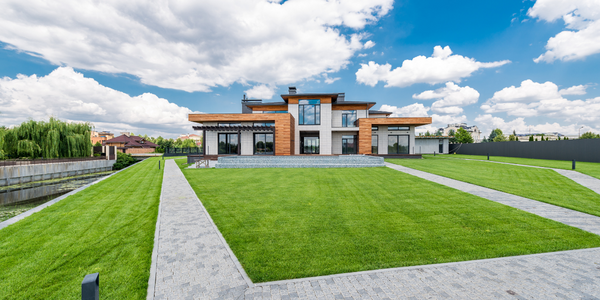
Case Study
Bellas Landscaping
Leading landscaping firm serving central Illinois streamlines operations with Samsara’s real-time fleet tracking solution: • 30+ vehicle fleet includes International Terrastar dump trucks and flatbeds, medium- and light-duty pickups from Ford and Chevrolet. Winter fleet includes of snow plows and salters.
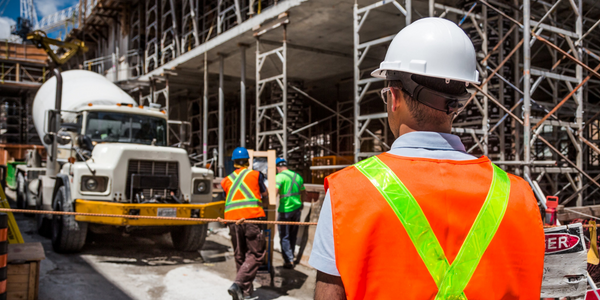
Case Study
Condition Based Monitoring for Industrial Systems
A large construction aggregate plant operates 10 high horsepower Secondary Crusher Drive Motors and associated conveyor belts, producing 600 tons of product per hour. All heavy equipment requires maintenance, but the aggregate producer’s costs were greatly magnified any time that the necessary maintenance was unplanned and unscheduled. The product must be supplied to the customers on a tight time schedule to fulfill contracts, avoid penalties, and prevent the loss of future business. Furthermore, a sudden failure in one of the drive motors would cause rock to pile up in unwanted locations, extending the downtime and increasing the costs.Clearly, preventative maintenance was preferable to unexpected failures. So, twice each year, the company brought in an outside vendor to attach sensors to the motors, do vibration studies, measure bearing temperatures and attempt to assess the health of the motors. But that wasn’t enough. Unexpected breakdowns continued to occur. The aggregate producer decided to upgrade to a Condition Based Monitoring (CBM) sensor system that could continually monitor the motors in real time, apply data analytics to detect changes in motor behavior before they developed into major problems, and alert maintenance staff via email or text, anywhere they happened to be.A wired sensor network would have been cost prohibitive. An aggregate plant has numerous heavy vehicles moving around, so any cabling would have to be protected. But the plant covers 400 acres, and the cable would have to be trenched to numerous locations. Cable wasn’t going to work. The aggregate producer needed a wireless solution.