Warehouse Automation
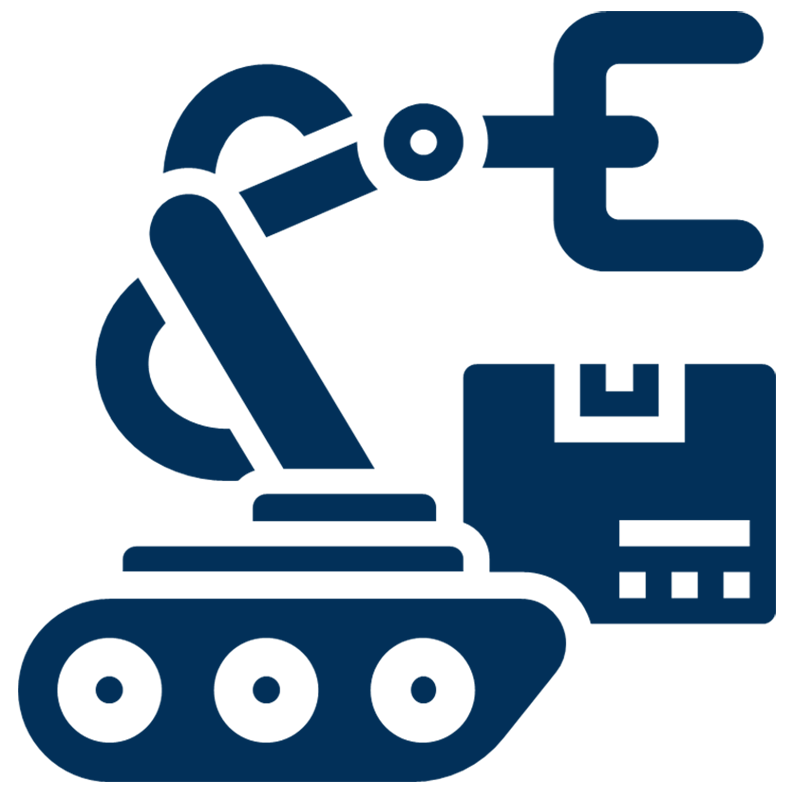
Warehouse automation is the application of specialized equipment and storage and retrieval systems to automate warehousing tasks previously handled by manual labor. Warehouse automation takes many forms, including machines and robots that aid workers with processes related to inventory handling, sensors that track goods, and software that automates record keeping. Leveraging warehouse automation solutions can help warehouses increase productivity, improve the accuracy of inventory records, reduce labor costs, and improve safety.
- Transportation
- Equipment & Machinery
- Logistics & Warehousing
The logistics automation market is estimated to be USD 46.22 Billion in 2018 and is projected to reach USD 80.64 Billion by 2023, at a CAGR of 11.8% during the forecast period
Source: Markets & Markets
How does warehouse automation impact an organization’s performance?
Warehouse automation can improve the efficiency of an organization's operations, resulting in lower operational costs, improved throughput, increased flexibility, real-time visibility into workflows, and the ability to forecast with greater accuracy. Several specific examples of efficiency gains include:
- Reduced energy usage: automated warehouses take up less square footage per volume of goods managed. As a result, they typically require less energy to light, heat and cool. And they use less energy to move goods by streamlining operational flow.
- Reduced staffing: significantly fewer workers are required in an automated warehouse. In many e-commerce warehouses, there are large segments of the process where people are only involved in system management, not in moving products.
- Improved visibility: RFID technology allows for the real-time tracking of goods that enter and leave the warehouse, resulting in tighter inventory control and the ability to dynamically modify orders or order priority. In addition, AS/RS technology minimizes storage space while maximizing the handling of the inventory’s mix of fast, intermediate, and slow-moving products.
- Greener packaging: the use of automation processes has played an important role in making environmentally friendly packaging possible. Packaging and warehouse operations can be jointly optimized to reduce packaging material while ensuring durability throughout the process.
- Reduced product damage: the consistent, predictable and smooth handling of products via an automated system reduces the potential for product damage. In addition, automated product selection is more accurate than human selection, less energy is utilized to facilitate the return of products picked and shipped in error.
- Greener profits: warehouses automation are the ability to improve productivity and reduce costs. Automation technologies have also been shown to have a positive effect on the environment makes warehouse automation a win-win prospect for the right business.
Operations Managers: Operations managers oversee the implementation and management of warehouse automation systems. They are responsible for evaluating automation technologies, optimizing warehouse layouts, and coordinating with IT and logistics teams to ensure seamless integration and operation of automated systems.
Warehouse Staff: Warehouse staff, including supervisors, pickers, packers, and logistics personnel, interact directly with automated systems in daily operations. They receive training on using automated equipment, monitor system performance, and troubleshoot any issues to ensure smooth functioning of the warehouse.
IT and Engineering Teams: IT and engineering teams play a crucial role in designing, implementing, and maintaining warehouse automation systems. They develop software solutions, integrate hardware components, and provide technical support to ensure the reliability, security, and efficiency of automated warehouse operations.
What are the components of smart warehouse systems?
Smart warehouse systems involve several interconnected technologies working together. Each of these components has its own distinct tasks that automate a crucial piece of your warehouse operation:
- Robotics: today’s warehousing robots are typically used for the storage and retrieval of goods within the warehouse.
- Radio-Frequency Identification (RFID): is an advanced method of maintaining inventory control. RFID involves placing a digital tag on goods and packages that come into a warehouse, replacing paper labels.
- Artificial Intelligence: it reduces errors and costs while increasing productivity. In warehousing specifically, AI has a lot of uses during every stage of the process.
- The Internet of Things: IoT is essential to the various components of smart warehouse systems working together properly. This means that robots can communicate with RFID scanners, which can communicate with conveyors, which can communicate with a warehouse management system (WMS), etc.
- Warehouse Management Systems: these software solutions help you collect, manage and view all kinds of data about your warehouse operations. This allows you to keep track of how efficient your warehouse’s day-to-day operations are running.
What different systems we can use in Warehouse Automation?
Warehouses can be automated in a number of ways, from automating operations like picking, barcode labels and scanning, and vehicles, to automating back-office processes.
- Goods-to-person technologies (GTP): GTP technologies are picking solutions that bring items to the worker, rather than requiring workers to travel to the items that need to be picked.
- Automated storage and retrieval systems (AS/RS): automated storage and retrieval systems (AS/RS) are one type of GTP technology. This warehouse technology automatically brings goods out of and then places them back into storage.
- Pick-to-light systems: in pick-to-light systems, operators scan barcodes as LED displays to illuminate to guide them to the correct storage location and to indicate how many items should be picked.
- Commerce fulfillment situations to address their high-volume, high-labor requirements.
What can we improve with Data Warehouse Automation?
Data Warehouse Automation improves the time-to-value and cost-to-value aspects of data warehousing by providing a simplified capture of the data warehouse design, providing automated builds (generating code), automating deployment, automating batch execution of the ETL code on the server and automating monitoring and execution of the batch execution. Essentially it provides a reliable pre-built data warehouse model that can be tapped and customized to suit individual organizational needs.
What data points are typically collected by the system?
In order to find the right information, many warehouses are using Inventory Management Systems. These are used to monitor inventory levels as well as orders and deliveries. The system tells you when you are likely to run out of stock so that you can order items in advance.
Some advantages of inventory management software give companies:
- Updated data: real-time data on inventory conditions and levels.
- Security Data: company managers can grant employees enough information access to receive products, make orders, transfer products and do other tasks without compromising company security.
- Insight into trends: tracking where products are stocked, which suppliers they come from, and the length of time they are stored is made possible with this system. By analyzing such data, companies can control inventory levels and maximize the use of warehouse space.
What business challenges could impact Warehouse Automation deployment?
- Selection of the right product: nowadays, there are many automation products available in the market for every process in the warehouse. But one should identify which one is best suitable for their operation.
- Silo working: any company going for automation must look at supply chain as a complete umbrella and not just a warehouse (where implementation of automation is planned).
- Start small and build a scalable solution: the path to advanced automation sometimes involves going through each level of automation sequentially as the business matures.
- Ever changing business requirements: with frequent changes in SKUs or addition of new products or changes or fluctuation in demands, there is a direct impact on the design of an automated system developed for the warehouse. Companies must design the automation system considering future demand for operation. Also, it should be easily scalable and modular.
- Change Management: one of the major challenges in implementing automation in any warehouse is change management because business processes and workflows need to customize with the implementation of automation.
- Say no to “one size fits all”: every warehouse has some unique characteristics and before replicating any automation system, companies should carefully evaluate all the checkpoints and then go for implementation.
Case Studies.
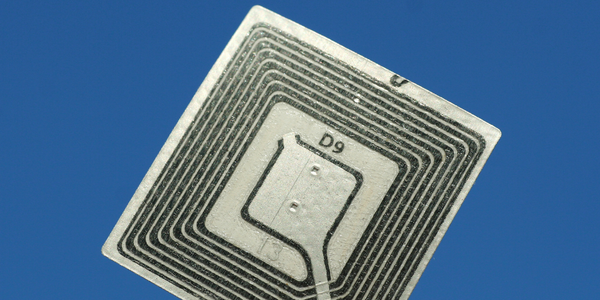
