Customer Company Size
Large Corporate
Region
- Europe
Country
- France
Product
- Wonderware ActiveFactory
- Wonderware InTouch HMI
- Wonderware Historian
Tech Stack
- Automation Software
- Data Acquisition
- HMI Interface
Implementation Scale
- Enterprise-wide Deployment
Impact Metrics
- Productivity Improvements
- Cost Savings
Technology Category
- Application Infrastructure & Middleware - Data Exchange & Integration
- Application Infrastructure & Middleware - Middleware, SDKs & Libraries
Applicable Industries
- Chemicals
Applicable Functions
- Discrete Manufacturing
Use Cases
- Process Control & Optimization
- Track & Trace of Assets
Services
- System Integration
- Software Design & Engineering Services
About The Customer
Bayer CropScience AG is a subsidiary of Bayer AG, an international group with core businesses in the health, nutrition and high-performance materials sectors. With annual sales figures of about 6.4 billion euro (2008), Bayer CropScience is leading the way in worldwide innovation in the fields of crop protection, nonagricultural pest management, seeds and plant biotechnologies. The company offers an extensive range of complementary products and services for modern and sustainable agriculture, as well as solutions for non-agricultural applications. Bayer CropScience has invested nearly 10 million euro at La Dargoire over the last two years in order to provide the existing laboratories with state-of-the-art equipment. The Biology department has benefitted from this investment with the creation of a new, fully-robotized system for large-scale testing of the effectiveness of new molecules on plant diseases.
The Challenge
Bayer CropScience AG, a subsidiary of Bayer AG, is a leading innovator in the fields of crop protection, nonagricultural pest management, seeds and plant biotechnologies. The company has invested nearly 10 million euro at La Dargoire over the last two years to provide the existing laboratories with state-of-the-art equipment. The Biology department has benefitted from this investment with the creation of a new, fully-robotized system for large-scale testing of the effectiveness of new molecules on plant diseases. The FROGSS (Fungicide Rotating Greenhouse Spraying System) project was born. Its functional scope concerning the steering monitoring solution remains to be defined. The company requested a tool that was able to change easily according to needs identified during the course of the project, without jeopardizing what already existed. Their options were quickly narrowed to a Wonderware solution which offered a modular and open architecture based on market standards.
The Solution
The FROGSS project automates several processes including spraying of plant sets from a loading zone, drying of sprayed solutions in a drying tunnel, classification of plants, by disease, in trolleys, washing and storing of the sets used in a storage zone, transporting of sets to the various zones mentioned above, and identification of treated sets and pots. The sequencing of all of these treatments is called a “Run.” This automation process implements several elements: computers, automatic devices, conveyors, robotic arms, a LiquidHandler, trolleys, carts, doors, valves, cylinders, nozzles, elevators, lifts, shafts, motors, pumps, cells, barcode readers and DataMatrix code and readers. In addition to automating the process, traceability is accomplished throughout the entire installation from taking the set, to arranging the pots, including spraying. The IT architecture is built around a Wonderware solution that interfaces with the Bayer CropScience management system (BCS). The solution, developed with the Wonderware InTouch HMI (Human Machine Interface) and Wonderware Historian allows the following functions to be provided: Representation of the process structured in the form of block diagrams, Real-time acquisition of process parameters, Visualization of safety elements, Acquisition of safety data, Alarm management, Recording and sorting of past events or alarms and for those currently in progress, Management of manufacturing program parameters, Configuration for the “Run”, Traceability management, Exchanges with the BCS system.
Operational Impact
Case Study missing?
Start adding your own!
Register with your work email and create a new case study profile for your business.
Related Case Studies.
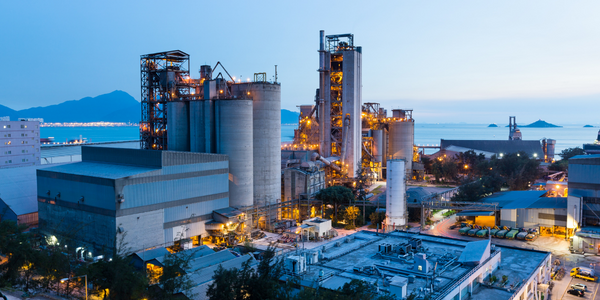
Case Study
Honeywell - Tata Chemicals Improves Data Accessibility with OneWireless
Tata was facing data accessibility challenges in the cement plant control room tapping signals from remote process control areas and other distant locations, including the gas scrubber. Tata needed a wireless solution to extend its control network securely to remote locations that would also provide seamless communication with existing control applications.
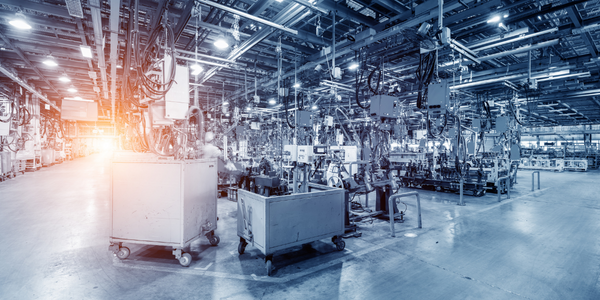
Case Study
Advanced Elastomer Systems Upgrades Production
In order to maintain its share of the international market for thermoplastic elastomers AES recently expanded its Florida plant by adding a new production line. While the existing lines were operating satisfactorily using a PROVOX distributed control system with traditional analog I/O, AES wanted advanced technology on the new line for greater economy, efficiency, and reliability. AES officials were anxious to get this line into production to meet incoming orders, but two hurricanes slowed construction.
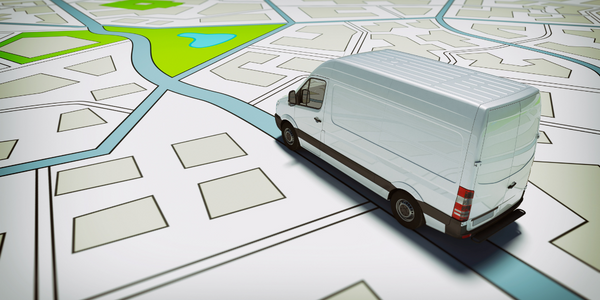
Case Study
Wireless GPS Tracking & Security Monitoring
Enhancing the security of hazardous freight and ensuring compliance with Homeland Security’s Transportation Security Administration mandate that all trains carrying chemicals capable of creating a toxic inhalation condition are equipped with on-board safety monitoring systems.
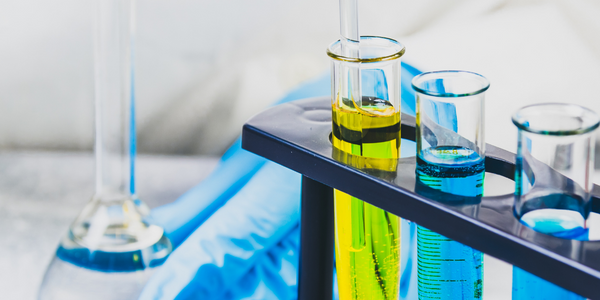
Case Study
Field Device Asset Management For Chemical Company in China
Chinese chemical subsidiary of multinational corporation serves customers throughout the world. Sales offices and research and technology centers are strategically located to provide rapid response to customer requests. Just two workers were assigned to maintain thousands of intelligent instruments in three production units, so they could do little more than react to device issues as they appeared. This costly maintenance method inevitably led to unexpected downtime when a critical instrument failed. Plant management recognized the need to change from reactive to predictive maintenance for all assets, including instruments and control valves, but help was needed in implementing such a technology-based initiative.
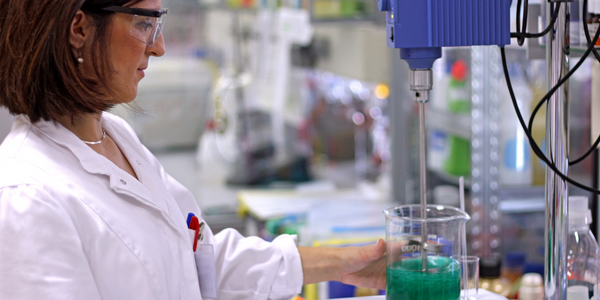
Case Study
Industrial Workforce Mobility for Improved Safety & Operations
Huntsman Corporation, a global manufacturer and marketer of differentiated chemicals, undertook an aggressive program to eliminate injuries, product defects, and environmental releases at their Port Neches facility. Termed “Project Zero”, this program required a completely mobile solution to empower operations and maintenance personnel to capture defects, track work progress and make process and safety related decisions in real-time.