Customer Company Size
Large Corporate
Region
- America
Country
- Canada
Product
- Avantis.PRO Enterprise Asset Management
Tech Stack
- Database Management
- Middleware
Implementation Scale
- Enterprise-wide Deployment
Impact Metrics
- Productivity Improvements
- Cost Savings
- Customer Satisfaction
Technology Category
- Functional Applications - Enterprise Asset Management Systems (EAM)
Applicable Industries
- Utilities
- Cities & Municipalities
Applicable Functions
- Maintenance
- Procurement
Use Cases
- Water Utility Management
- Predictive Maintenance
- Inventory Management
Services
- System Integration
- Software Design & Engineering Services
About The Customer
The City of Toronto was created on January 1, 1998, through the amalgamation of the seven separate entities of the former Municipality of Metropolitan Toronto. The City provides a full range of services to the more than 2.5 million residents of Toronto through its six major departments and a number of agencies, boards, and commissions. Toronto is the largest city in Canada and the 5th largest city in North America. The Water and Wastewater Division of Toronto Works and Emergency Services (WES) is responsible for producing and distributing potable water across the City as well as collecting and treating the City’s wastewater. The division is involved in a broad improvement initiative called the Works Best Practices Program (WBPP), which is focused on developing a highly efficient organizational structure through the application of redesigned work practices and the acquisition of new process control and information systems.
The Challenge
The Water and Wastewater Division of Toronto Works and Emergency Services (WES) was operating with outdated preventive maintenance and inventory programs that were developed internally. Each facility had its own version of these programs, and the functionality was very limited. The division was spending most of its time in a reactive maintenance mode, which was identified as a productivity gap. The division aimed to shift towards a more proactive maintenance approach, which required advanced business tools and information systems.
The division was involved in a broad improvement initiative called the Works Best Practices Program (WBPP). The WBPP aimed to develop a highly efficient organizational structure through the application of redesigned work practices and the acquisition of new process control and information systems. An Enterprise Asset Management (EAM) system with full maintenance, inventory, and purchasing functionality was identified as a key component of the WBPP applications architecture.
The Solution
The Water and Wastewater Division of Toronto Works and Emergency Services (WES) implemented the AVEVA solution at the first site. The AVEVA solution met all of the WBPP’s EAM core functional requirements, including work management, inventory, and procurement. It easily adapted to the middleware enabled “integrated information environment” being implemented under the WBPP.
The AVEVA solution was central to the Division’s efforts to implement “Program-Driven Maintenance,” effectively moving from a largely reactive to a fully planned maintenance environment. Management could determine accurately and quickly the costs of performing maintenance at water and wastewater operating facilities. They could review work history and generally do better planning and make better maintenance and business decisions. Using the AVEVA solution, the Division began to identify real savings by maintaining optimized inventory levels and improving replenishment procedures.
The AVEVA solution was central to the Division’s efforts to implement “Program-Driven Maintenance,” effectively moving from a largely reactive to a fully planned maintenance environment. Management could determine accurately and quickly the costs of performing maintenance at water and wastewater operating facilities. They could review work history and generally do better planning and make better maintenance and business decisions. Using the AVEVA solution, the Division began to identify real savings by maintaining optimized inventory levels and improving replenishment procedures.
Operational Impact
Case Study missing?
Start adding your own!
Register with your work email and create a new case study profile for your business.
Related Case Studies.
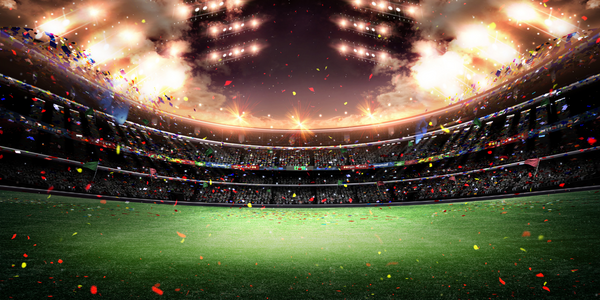
Case Study
Turning A Stadium Into A Smart Building
Honeywell created what it called the “intelligent system” for the National Stadium in Beijing, China, turning the venue for the opening and closing events at the 2008 Summer Olympics into a “smart building.” Designed by highly controversial artist Ai Weiwei, the “Bird’s Nest” remains one of the most impressive feats of stadium architecture in the world. The 250,000 square meter structure housed more than 100,000 athletes and spectators at a time. To accommodate such capacity, China turned to Honeywell’s EBI Integrated Building Management System to create an integrated “intelligent system” for improved building security, safety and energy efficiency.

Case Study
IoT Solutions for Smart City | Internet of Things Case Study
There were several challenges faced: It is challenging to build an appliance that can withstand a wide range of voltage fluctuations from as low at 90v to as high as 320v. Since the device would be installed in remote locations, its resilience was of paramount importance. The device would have to deal with poor network coverage and have the ability to store and re-transmit data if networks were not available, which is often the case in rural India. The device could store up to 30 days of data.
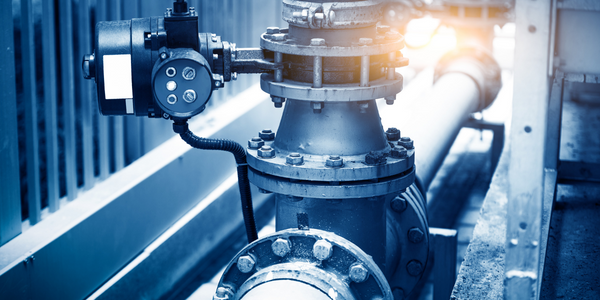
Case Study
Automation of the Oguz-Gabala-Baku water pipeline, Azerbaijan
The Oguz-Gabala-Baku water pipeline project dates back to plans from the 1970’s. Baku’s growth was historically driven by the booming oil industry and required the import of drinking water from outside of the city. Before the construction of the pipeline, some 60 percent of the city’s households received water for only a few hours daily. After completion of the project, 75 percent of the two million Baku residents are now served around the clock with potable water, based on World Health Organization (WHO) standards. The 262-kilometer pipeline requires no pumping station, but uses the altitude differences between the Caucasian mountains and the capital to supply 432,000 m³/d to the Ceyranbatan water reservoir. To the people of Baku, the pipeline is “the most important project not only in 2010, but of the last 20 years.”
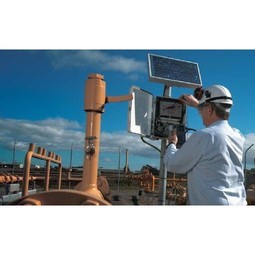
Case Study
GPRS Mobile Network for Smart Metering
Around the world, the electricity supply industry is turning to ‘smart’ meters to lower costs, reduce emissions and improve the management of customer supplies. Smart meters collect detailed consumption information and using this feedback consumers can better understand their energy usage which in turn enables them to modify their consumption to save money and help to cut carbon emissions. A smart meter can be defined in many ways, but generally includes an element of two-way communication between the household meter and the utility provider to efficiently collect detailed energy usage data. Some implementations include consumer feedback beyond the energy bill to include online web data, SMS text messages or an information display in consumers’ premises. Providing a cost-effective, reliable communications mechanism is one of the most challenging aspects of a smart meter implementation. In New Zealand, the utilities have embraced smart metering and designed cost effective ways for it to be implemented. The New Zealand government has encouraged such a move to smart metering by ensuring the energy legislation is consistent with the delivery of benefits to the consumer while allowing innovation in this area. On the ground, AMS is a leader in the deployment of smart metering and associated services. Several of New Zealand’s energy retailers were looking for smart metering services for their residential and small business customers which will eventually account for over 500,000 meters when the multi-year national deployment program is concluded. To respond to these requirements, AMS needed to put together a solution that included data communications between each meter and the central data collection point and the solution proposed by Vodafone satisfied that requirement.
.png)
Case Study
Smart Street Light Network (Copenhagen)
Key stakeholders are taking a comprehensive approach to rethinking smart city innovation. City leaders have collaborated through partnerships involving government, research institutions and solution providers. The Copenhagen Solutions Lab is one of the leading organizations at the forefront of this movement. By bringing together manufacturers with municipal buyers, the Copenhagen Solutions Lab has catalyzed the development and deployment of next-generation smart city innovations. Copenhagen is leveraging this unique approach to accelerate the implementation of smart city solutions. One of the primary focus areas is LED street lighting.
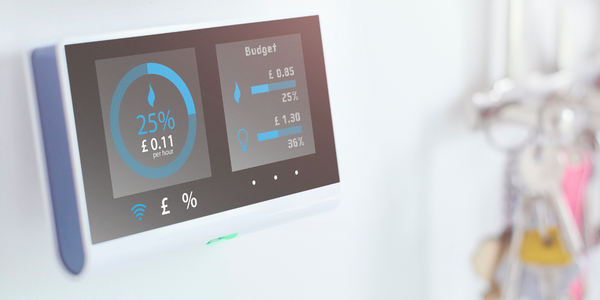
Case Study
NB-IoT connected smart meters to improve gas metering in Shenzhen
Shenzhen Gas has a large fleet of existing gas meters, which are installed in a variety of hard to reach locations, such as indoors and underground, meaning that existing communications networks have struggled to maintain connectivity with all meters. The meter success rate is low, data transmissions are so far unstable and power consumption is too high. Against this background, Shenzhen Gas, China Telecom, Huawei, and Goldcard have jointly trialed NB-IoT gas meters to try and solve some of the challenges that the industry faces with today’s smart gas meters.