Technology Category
- Analytics & Modeling - Digital Twin / Simulation
- Sensors - Gas Sensors
Applicable Industries
- Automotive
- Equipment & Machinery
Applicable Functions
- Product Research & Development
- Sales & Marketing
Use Cases
- Time Sensitive Networking
- Virtual Prototyping & Product Testing
Services
- Testing & Certification
About The Customer
MAHLE is a Tier 1 automotive systems supplier based in Stuttgart, Germany, with over 64,000 employees globally expected to generate sales of over $13 billion in 2014. The company maintains 10 different research and development (R&D) centers around the world, including locations in China, Japan, Brazil, England, India, and the United States. In North America, MAHLE generated sales of over $2.6 billion in 2013, boasting 29 locations and more than 10,000 employees. All of MAHLE’s business units are represented in the region, Engine Systems and Components, Filtration and Engine Peripherals, as well as Thermal Management. All light vehicle and truck OEMs with production operations in North America are supplied by MAHLE. The company serves the independent spare parts market though its Aftermarket business unit. In addition, MAHLE services motorsports customers in the region.
The Challenge
MAHLE, a leading automotive systems supplier, faced a challenge in making their simulation results reporting consistent, thorough, and simpler to perform. The company conducts simulations for pistons, connecting rods, and pins, with pistons representing the majority of the group's work. The complexity of pistons, which must withstand high temperatures and huge inertia loads, introduces many variables into the design process. Six different engineers were creating slightly different reports, leading to variations in how the simulation story was being told to customers. The main question to be answered by the simulation is whether the piston will survive the engine test. These tests are quite expensive, and a pre-production piston needs to be tested before it is put into the engine to save physical testing costs and to enable more design iterations. The complexity of the evaluation is further increased by factors such as lightweight pistons, high-efficiency engines, highly-loaded four-cylinder engines, more variability, and different materials.
The Solution
Altair ProductDesign’s team suggested an implementation of Automated Reporting Director (ARD) to help MAHLE streamline reporting activity. ARD is a configurable and customizable reporting solution which is embedded in HyperView and loops over all defined groups and load cases, creating a single report page for each combination. ARD automates the detection of result maxima or hot spots, best view selection, creation of notes and legends, and highlights the most interesting results in an interactive tab. The tool is also flexible, allowing the analyst to step through each page before exporting it into PowerPoint or another desired format. Through an intuitive user interface, ARD allows the analyst to post-process results with given criteria, generate interactive overview result tables highlighting critical results, compare results between model iterations, and export results using preferred, customizable reporting templates.
Operational Impact
Quantitative Benefit
Case Study missing?
Start adding your own!
Register with your work email and create a new case study profile for your business.
Related Case Studies.
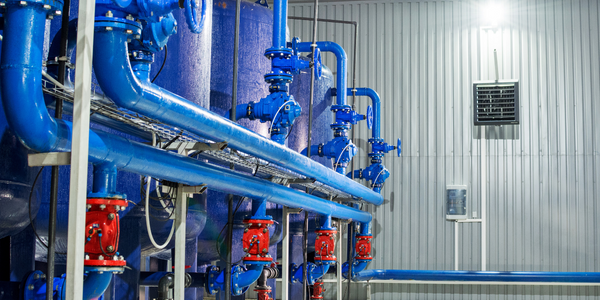
Case Study
Smart Water Filtration Systems
Before working with Ayla Networks, Ozner was already using cloud connectivity to identify and solve water-filtration system malfunctions as well as to monitor filter cartridges for replacements.But, in June 2015, Ozner executives talked with Ayla about how the company might further improve its water systems with IoT technology. They liked what they heard from Ayla, but the executives needed to be sure that Ayla’s Agile IoT Platform provided the security and reliability Ozner required.
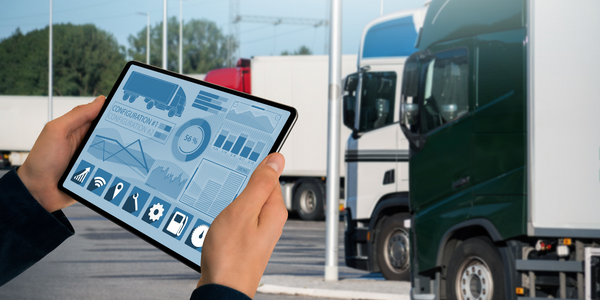
Case Study
IoT enabled Fleet Management with MindSphere
In view of growing competition, Gämmerler had a strong need to remain competitive via process optimization, reliability and gentle handling of printed products, even at highest press speeds. In addition, a digitalization initiative also included developing a key differentiation via data-driven services offers.
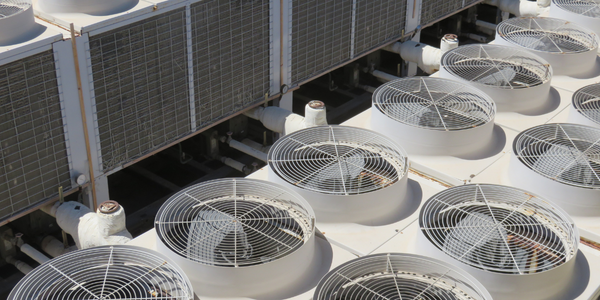
Case Study
Predictive Maintenance for Industrial Chillers
For global leaders in the industrial chiller manufacturing, reliability of the entire production process is of the utmost importance. Chillers are refrigeration systems that produce ice water to provide cooling for a process or industrial application. One of those leaders sought a way to respond to asset performance issues, even before they occur. The intelligence to guarantee maximum reliability of cooling devices is embedded (pre-alarming). A pre-alarming phase means that the cooling device still works, but symptoms may appear, telling manufacturers that a failure is likely to occur in the near future. Chillers who are not internet connected at that moment, provide little insight in this pre-alarming phase.
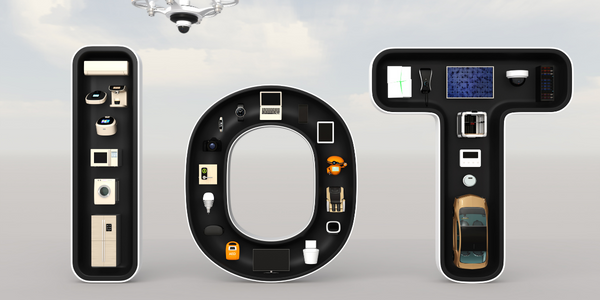
Case Study
Premium Appliance Producer Innovates with Internet of Everything
Sub-Zero faced the largest product launch in the company’s history:It wanted to launch 60 new products as scheduled while simultaneously opening a new “greenfield” production facility, yet still adhering to stringent quality requirements and manage issues from new supply-chain partners. A the same time, it wanted to increase staff productivity time and collaboration while reducing travel and costs.
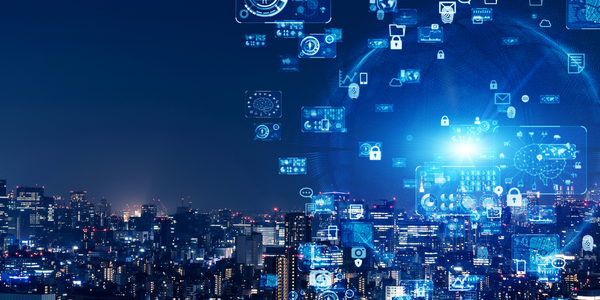
Case Study
Integration of PLC with IoT for Bosch Rexroth
The application arises from the need to monitor and anticipate the problems of one or more machines managed by a PLC. These problems, often resulting from the accumulation over time of small discrepancies, require, when they occur, ex post technical operations maintenance.
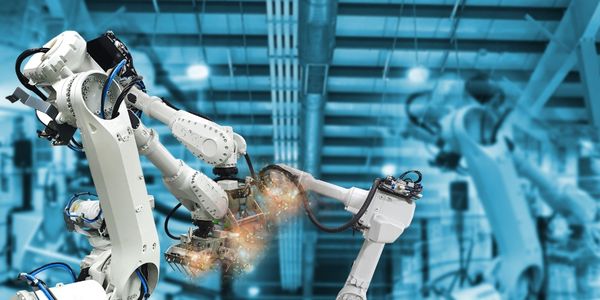
Case Study
Robot Saves Money and Time for US Custom Molding Company
Injection Technology (Itech) is a custom molder for a variety of clients that require precision plastic parts for such products as electric meter covers, dental appliance cases and spools. With 95 employees operating 23 molding machines in a 30,000 square foot plant, Itech wanted to reduce man hours and increase efficiency.