Plascon Paints a Brighter Production Picture with Help from Invensys Operations Management Solutions
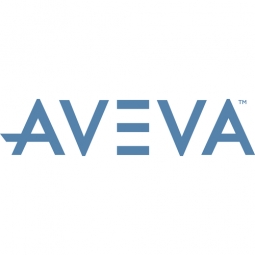
Customer Company Size
Large Corporate
Region
- Africa
Country
- South Africa
Product
- Wonderware InBatch
- Wonderware InTouch HMI
- Wonderware Historian
- Wonderware System Platform
Tech Stack
- SCADA technology
- PLC
Implementation Scale
- Enterprise-wide Deployment
Impact Metrics
- Productivity Improvements
- Cost Savings
Technology Category
- Functional Applications - Manufacturing Execution Systems (MES)
- Functional Applications - Remote Monitoring & Control Systems
Applicable Industries
- Chemicals
Applicable Functions
- Discrete Manufacturing
- Quality Assurance
Use Cases
- Manufacturing System Automation
- Predictive Quality Analytics
Services
- System Integration
- Software Design & Engineering Services
About The Customer
Plascon is a successful paint and coatings company that manufactures paint in a specific color palette, with batch consistency and uniformity being critical to their operations. Strict recipe control, traceable batch parameters, and consistent product quality are the hallmarks of this company. Plascon first implemented Wonderware InBatch software in 1995 and as they expanded their line of paint supplies to include premium decorative and road marking paint, they realized the need to upgrade the technology. The company is designed as a flexible manufacturing facility to address challenging production schedules and chose to upgrade to the latest version of Wonderware InTouch HMI. The company's goal for the upgrade strategy was to focus on producing products of the highest quality, while maintaining and meeting tight production schedules.
The Challenge
Plascon, a successful paint and coatings company, was facing challenges in maintaining batch consistency and uniformity in their manufacturing process. The company had initially implemented Wonderware InBatch software in 1995, but as they expanded their product line, they realized the need for an upgrade. The existing technology infrastructure could not keep up with Plascon’s expanding business operations, leading to poor production efficiency, lack of detailed traceability, and a multitude of errors inherent in manual processes. Production scheduling became more difficult, and automated batch reports detailing the productivity process could no longer be produced for plant management. The new software infrastructure had to address key operational issues such as clearly defined batch recipes, detailed displays of batch status, and a reliable, semi-automatic mode of batching.
The Solution
Plascon chose to upgrade their existing Wonderware InBatch software and also implement the latest version of Wonderware InTouch HMI. These new Invensys software components were integrated with Wonderware System Platform, enabling Plascon to establish a single scalable SCADA technology platform that would allow the company to perform system upgrades more quickly and easily throughout the entire manufacturing operation. Wonderware InBatch enables plant operators and managers to accurately identify the proper recipes and observe the paint mixing process in real-time on a display screen to ensure successful batch execution and completion. It also provides material genealogy data and Web-based reporting to simplify monitoring and measurement of the overall manufacturing process. Wonderware System Platform provides industrial manufacturing processes with a single, scalable platform for all SCADA, supervisory HMI and MES requirements, enabling Plascon to more easily maintain and manage all of the functional capabilities required within its manufacturing operation.
Operational Impact
Case Study missing?
Start adding your own!
Register with your work email and create a new case study profile for your business.
Related Case Studies.
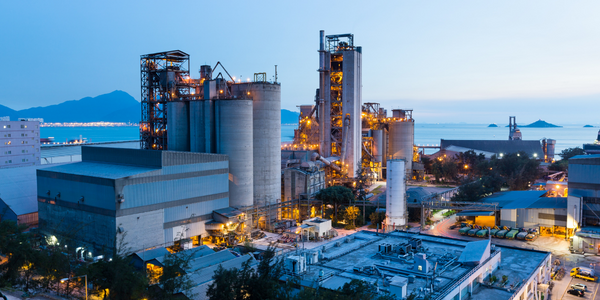
Case Study
Honeywell - Tata Chemicals Improves Data Accessibility with OneWireless
Tata was facing data accessibility challenges in the cement plant control room tapping signals from remote process control areas and other distant locations, including the gas scrubber. Tata needed a wireless solution to extend its control network securely to remote locations that would also provide seamless communication with existing control applications.
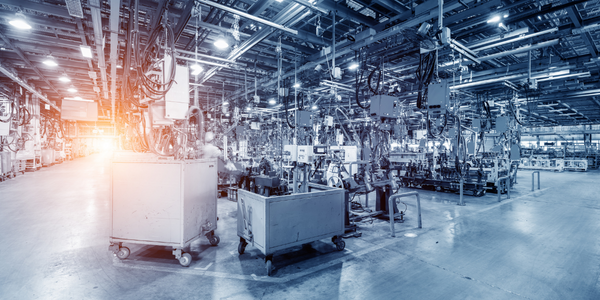
Case Study
Advanced Elastomer Systems Upgrades Production
In order to maintain its share of the international market for thermoplastic elastomers AES recently expanded its Florida plant by adding a new production line. While the existing lines were operating satisfactorily using a PROVOX distributed control system with traditional analog I/O, AES wanted advanced technology on the new line for greater economy, efficiency, and reliability. AES officials were anxious to get this line into production to meet incoming orders, but two hurricanes slowed construction.
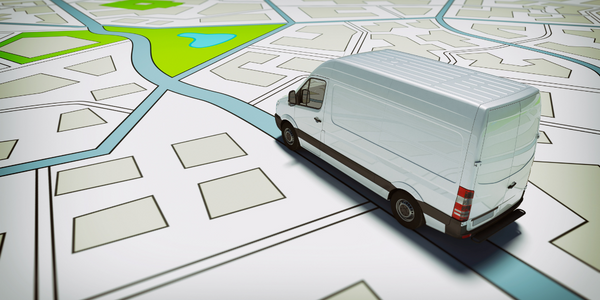
Case Study
Wireless GPS Tracking & Security Monitoring
Enhancing the security of hazardous freight and ensuring compliance with Homeland Security’s Transportation Security Administration mandate that all trains carrying chemicals capable of creating a toxic inhalation condition are equipped with on-board safety monitoring systems.
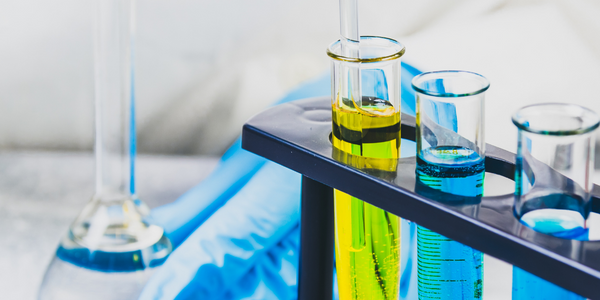
Case Study
Field Device Asset Management For Chemical Company in China
Chinese chemical subsidiary of multinational corporation serves customers throughout the world. Sales offices and research and technology centers are strategically located to provide rapid response to customer requests. Just two workers were assigned to maintain thousands of intelligent instruments in three production units, so they could do little more than react to device issues as they appeared. This costly maintenance method inevitably led to unexpected downtime when a critical instrument failed. Plant management recognized the need to change from reactive to predictive maintenance for all assets, including instruments and control valves, but help was needed in implementing such a technology-based initiative.
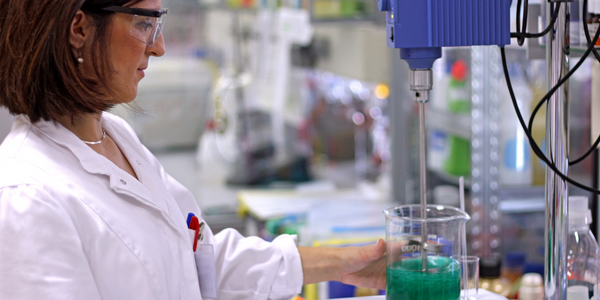
Case Study
Industrial Workforce Mobility for Improved Safety & Operations
Huntsman Corporation, a global manufacturer and marketer of differentiated chemicals, undertook an aggressive program to eliminate injuries, product defects, and environmental releases at their Port Neches facility. Termed “Project Zero”, this program required a completely mobile solution to empower operations and maintenance personnel to capture defects, track work progress and make process and safety related decisions in real-time.