Customer Company Size
Large Corporate
Region
- Europe
Country
- Germany
Product
- Alteryx
- Tableau
Tech Stack
- Data Analysis
- Data Visualization
- Automation
Implementation Scale
- Enterprise-wide Deployment
Impact Metrics
- Productivity Improvements
- Digital Expertise
Technology Category
- Analytics & Modeling - Data-as-a-Service
- Analytics & Modeling - Real Time Analytics
Applicable Functions
- Business Operation
Use Cases
- Predictive Maintenance
- Process Control & Optimization
Services
- Data Science Services
About The Customer
Siemens is one of the most important companies in Germany, established in October 1847. Today, the technology corporation is active in 190 countries, with 125 locations just in Germany. This company, which is traded on the DAX 30 exchange, has about 379,000 employees worldwide. The Siemens Gas and Power Division is one wheel in this huge drive. To ensure that all of the processes interact efficiently here, in 2016 Siemens launched a productivity offensive for power plant service.
The Challenge
The Siemens Gas and Power Division launched a productivity offensive for power plant service in 2016. The objective was to analyze areas where unnecessary costs, such as excessively high material expenses, could be prevented. With several thousand various measures, more than 5,000 different data sets, and over 8,000 employees in the business unit, the investigations were complex and time-consuming. The analyses were nearly obsolete by the time the results were available. The first step was to switch to Tableau to improve the visualization. However, the actual problem with the time-consuming and complicated provision of data was still not solved.
The Solution
The big change came about with Alteryx. Alteryx provided automation, so repetitive tasks, such as manually updating the data, are no longer necessary, and the employees can focus more on the analysis. In addition to the time saved, Alteryx also improved the quality of the analysis. Because the dashboards are automatically updated in three-hour cycles, the data is never outdated. Alteryx is user-friendly and easy to learn, these are two pivotal reasons that the employees like Alteryx so much. With Alteryx, employees in a wide variety of departments can be trained as citizen data scientists. In the case of the Siemens Gas and Power Unit, the software is mainly used in middle management for specific process optimization.
Operational Impact
Quantitative Benefit
Case Study missing?
Start adding your own!
Register with your work email and create a new case study profile for your business.
Related Case Studies.
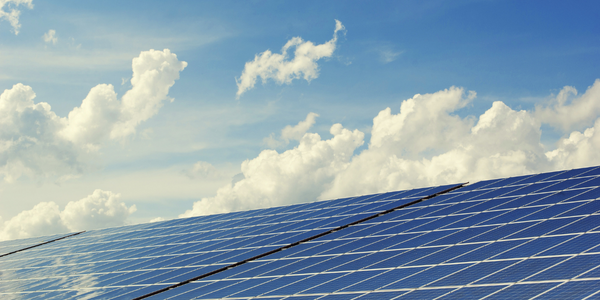
Case Study
Remote Monitoring & Predictive Maintenance App for a Solar Energy System
The maintenance & tracking of various modules was an overhead for the customer due to the huge labor costs involved. Being an advanced solar solutions provider, they wanted to ensure early detection of issues and provide the best-in-class customer experience. Hence they wanted to automate the whole process.
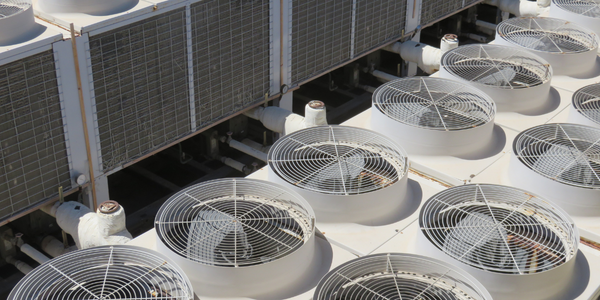
Case Study
Predictive Maintenance for Industrial Chillers
For global leaders in the industrial chiller manufacturing, reliability of the entire production process is of the utmost importance. Chillers are refrigeration systems that produce ice water to provide cooling for a process or industrial application. One of those leaders sought a way to respond to asset performance issues, even before they occur. The intelligence to guarantee maximum reliability of cooling devices is embedded (pre-alarming). A pre-alarming phase means that the cooling device still works, but symptoms may appear, telling manufacturers that a failure is likely to occur in the near future. Chillers who are not internet connected at that moment, provide little insight in this pre-alarming phase.
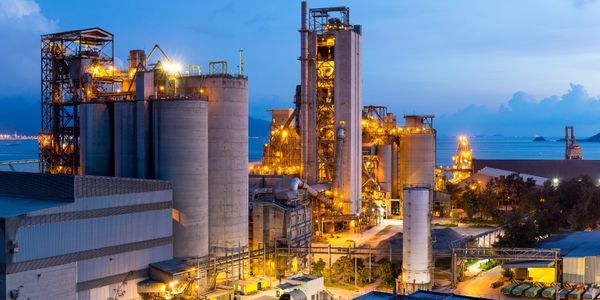
Case Study
System 800xA at Indian Cement Plants
Chettinad Cement recognized that further efficiencies could be achieved in its cement manufacturing process. It looked to investing in comprehensive operational and control technologies to manage and derive productivity and energy efficiency gains from the assets on Line 2, their second plant in India.
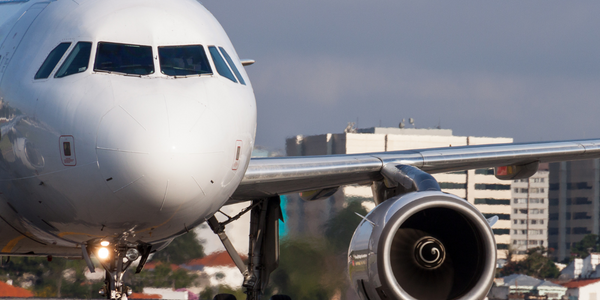
Case Study
Airbus Soars with Wearable Technology
Building an Airbus aircraft involves complex manufacturing processes consisting of thousands of moving parts. Speed and accuracy are critical to business and competitive advantage. Improvements in both would have high impact on Airbus’ bottom line. Airbus wanted to help operators reduce the complexity of assembling cabin seats and decrease the time required to complete this task.
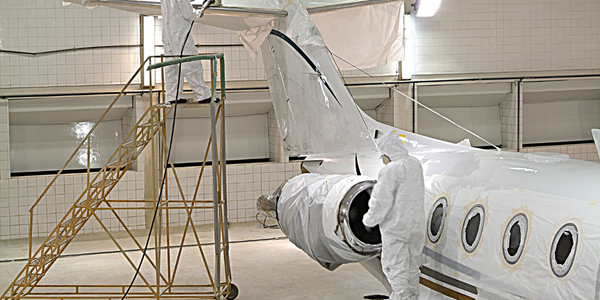
Case Study
Aircraft Predictive Maintenance and Workflow Optimization
First, aircraft manufacturer have trouble monitoring the health of aircraft systems with health prognostics and deliver predictive maintenance insights. Second, aircraft manufacturer wants a solution that can provide an in-context advisory and align job assignments to match technician experience and expertise.