Technology Category
- Functional Applications - Manufacturing Execution Systems (MES)
Applicable Industries
- Automotive
- Life Sciences
Applicable Functions
- Logistics & Transportation
- Product Research & Development
Use Cases
- Additive Manufacturing
- Rapid Prototyping
About The Customer
Monash Motorsport is a student-run organization based at Monash University’s largest campus in Clayton, Victoria. A team of 70 students designs, constructs and races an open-wheel racecar in Formula SAE, the world’s largest student engineering design competition with over 500 teams worldwide. In the Monash Motorsport team, students gain invaluable practical skills in their respective fields of both engineering and business, enriching their university experience and equipping them with knowledge that will allow them to prosper in their chosen career paths.
The Challenge
Monash Motorsport, a student-run organization based at Monash University, has been consistently improving the performance of their race car since their first Australian SAE Student Racing competition in 2000. The team was facing new weight and performance challenges at the end of 2013. They aimed to develop faster, lighter, and more innovative race cars while keeping development time and costs under control. The evolution of 3D printing presented a new technology that could help them build even lighter cars. However, it also created new development challenges since the 3D printed components are only as good as their design. The team had to conduct an optimization to find the ideal material distribution in the components while taking into account the additional manufacturing constraints of the additive manufacturing technology.
The Solution
Monash Motorsport employed Altair’s optimization technology OptiStruct to design and optimize a titanium upright, which was then produced using additive manufacturing technology from CSIRO. The use of Altair‘s HyperWorks Suite enabled a simulation driven design process and an optimal structural design of the component planned to be produced with additive manufacturing. Working within the constraints of the current geometry, the students created a design space in Altair‘s optimization tool OptiStruct. By applying boundary conditions such as loads and manufacturing constraints they ran a topology optimization and OptiStruct helped them to create a stiffer and lighter component structure. The students then used the OptiStruct design proposal, interpreted it and created a working CAD design. This design was then validated with a further Finite-Element Analysis, using multiple load cases.
Operational Impact
Quantitative Benefit
Case Study missing?
Start adding your own!
Register with your work email and create a new case study profile for your business.
Related Case Studies.
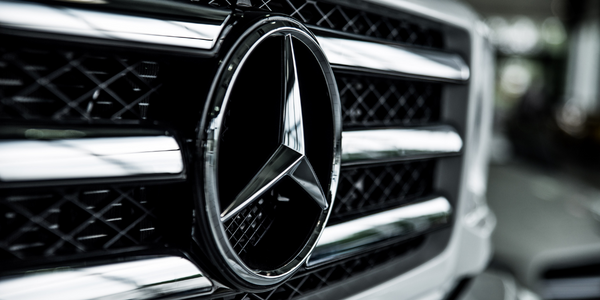
Case Study
Integral Plant Maintenance
Mercedes-Benz and his partner GAZ chose Siemens to be its maintenance partner at a new engine plant in Yaroslavl, Russia. The new plant offers a capacity to manufacture diesel engines for the Russian market, for locally produced Sprinter Classic. In addition to engines for the local market, the Yaroslavl plant will also produce spare parts. Mercedes-Benz Russia and his partner needed a service partner in order to ensure the operation of these lines in a maintenance partnership arrangement. The challenges included coordinating the entire maintenance management operation, in particular inspections, corrective and predictive maintenance activities, and the optimizing spare parts management. Siemens developed a customized maintenance solution that includes all electronic and mechanical maintenance activities (Integral Plant Maintenance).
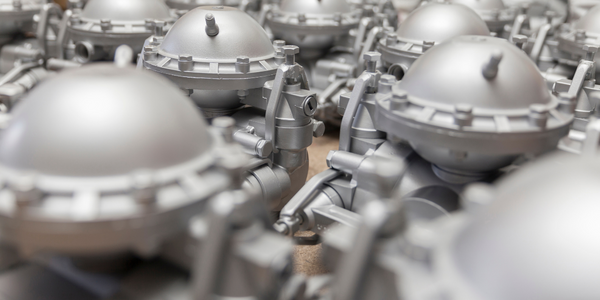
Case Study
Monitoring of Pressure Pumps in Automotive Industry
A large German/American producer of auto parts uses high-pressure pumps to deburr machined parts as a part of its production and quality check process. They decided to monitor these pumps to make sure they work properly and that they can see any indications leading to a potential failure before it affects their process.