Technology Category
- Analytics & Modeling - Digital Twin / Simulation
- Sensors - Temperature Sensors
Applicable Industries
- Equipment & Machinery
Applicable Functions
- Product Research & Development
- Quality Assurance
Use Cases
- Digital Twin
- Virtual Reality
Services
- Testing & Certification
About The Customer
Esterline Advanced Sensors is a leading provider of high precision solutions for aeronautics, including cockpit, airframe, and engine sensors, as well as derivative products for marine, defense, and the industrial sector. The company prides itself on its strong company culture, demonstrated by its 936 employees who are driven by high added-value customer service, reliability, and the best operational performance of their products. Esterline Advanced Sensors is a leader in the field of sensors for pressure, temperature, speed, torque, and analogue indicators. The company's ability to master programs from design to development to production and to work with partners in different fields of application makes it a tier one supplier.
The Challenge
Esterline Advanced Sensors, a leading provider of aeronautic sensors, faced a significant challenge in the development of their products. Each sensor is a unique project for a specific customer, with individual requirements that often change during the development process. This necessitates multiple iterations on design changes and intensive simulations to ensure the final product meets the customer's needs. The sensors, composed of several sub-parts and different materials, grow into complex models when prepared for simulation. The efficiency and reliability of the simulation heavily depend on the mesh features and quality of these models. The challenge was to quickly incorporate required modifications into the current model, create models from scratch, and quickly adopt modifications for design variants, all while maintaining high quality and reducing calculation time.
The Solution
To address these challenges, Esterline Advanced Sensors implemented HyperWorks, specifically HyperMesh, in the development of their aeronautic sensors. After creating a CAD model, the engineers use HyperMesh to prepare the models for different types of analysis. HyperMesh is a high-performance finite element pre-processor that provides a highly interactive and visual environment to create high-quality meshes and analyze product design performance. It distinguishes itself from other meshing tools by providing accurate meshes for many different commercially available solvers and simulation disciplines in a short time frame. The engineers then use these meshed models for various simulation tasks such as FE analysis, NVH simulation, and CFD analysis.
Operational Impact
Quantitative Benefit
Case Study missing?
Start adding your own!
Register with your work email and create a new case study profile for your business.
Related Case Studies.
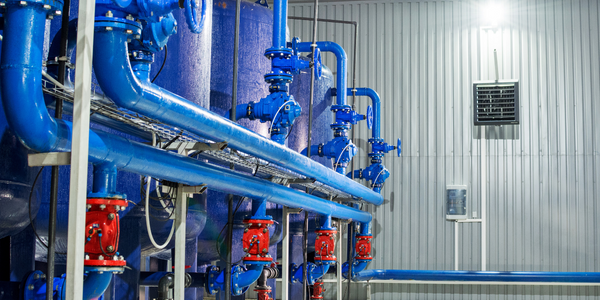
Case Study
Smart Water Filtration Systems
Before working with Ayla Networks, Ozner was already using cloud connectivity to identify and solve water-filtration system malfunctions as well as to monitor filter cartridges for replacements.But, in June 2015, Ozner executives talked with Ayla about how the company might further improve its water systems with IoT technology. They liked what they heard from Ayla, but the executives needed to be sure that Ayla’s Agile IoT Platform provided the security and reliability Ozner required.
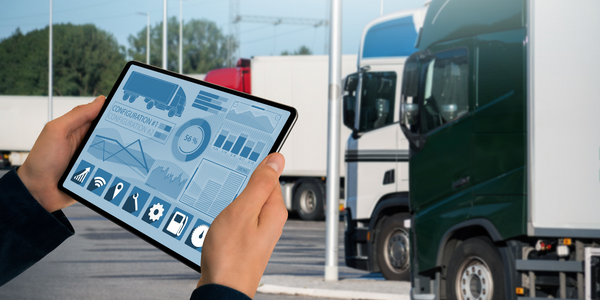
Case Study
IoT enabled Fleet Management with MindSphere
In view of growing competition, Gämmerler had a strong need to remain competitive via process optimization, reliability and gentle handling of printed products, even at highest press speeds. In addition, a digitalization initiative also included developing a key differentiation via data-driven services offers.
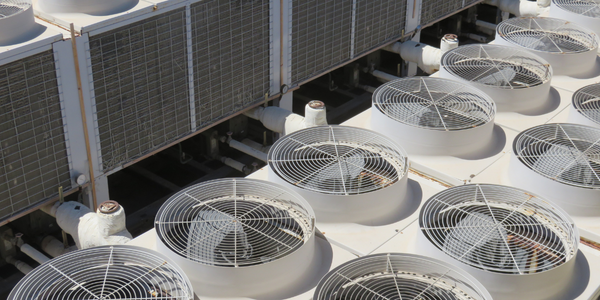
Case Study
Predictive Maintenance for Industrial Chillers
For global leaders in the industrial chiller manufacturing, reliability of the entire production process is of the utmost importance. Chillers are refrigeration systems that produce ice water to provide cooling for a process or industrial application. One of those leaders sought a way to respond to asset performance issues, even before they occur. The intelligence to guarantee maximum reliability of cooling devices is embedded (pre-alarming). A pre-alarming phase means that the cooling device still works, but symptoms may appear, telling manufacturers that a failure is likely to occur in the near future. Chillers who are not internet connected at that moment, provide little insight in this pre-alarming phase.
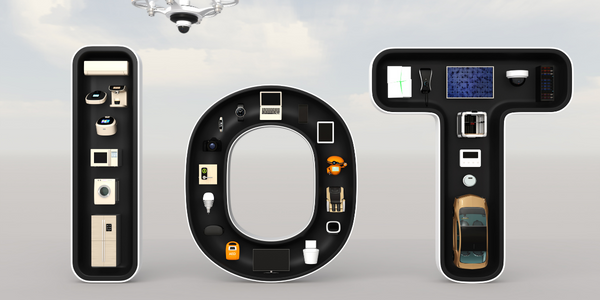
Case Study
Premium Appliance Producer Innovates with Internet of Everything
Sub-Zero faced the largest product launch in the company’s history:It wanted to launch 60 new products as scheduled while simultaneously opening a new “greenfield” production facility, yet still adhering to stringent quality requirements and manage issues from new supply-chain partners. A the same time, it wanted to increase staff productivity time and collaboration while reducing travel and costs.
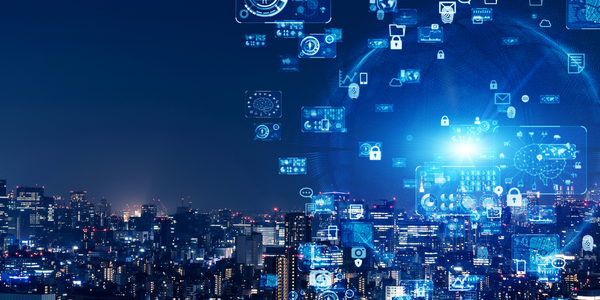
Case Study
Integration of PLC with IoT for Bosch Rexroth
The application arises from the need to monitor and anticipate the problems of one or more machines managed by a PLC. These problems, often resulting from the accumulation over time of small discrepancies, require, when they occur, ex post technical operations maintenance.
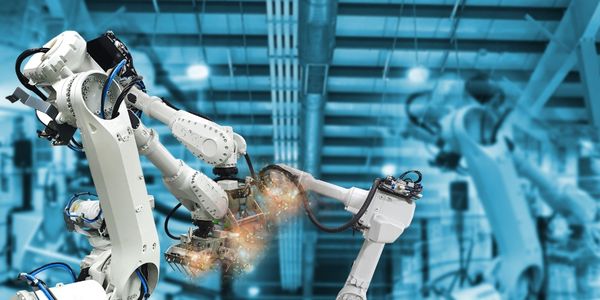
Case Study
Robot Saves Money and Time for US Custom Molding Company
Injection Technology (Itech) is a custom molder for a variety of clients that require precision plastic parts for such products as electric meter covers, dental appliance cases and spools. With 95 employees operating 23 molding machines in a 30,000 square foot plant, Itech wanted to reduce man hours and increase efficiency.