Customer Company Size
Mid-size Company
Region
- America
Country
- United States
Product
- System Platform
- Workflow Management
- Historian
- InTouch HMI
Tech Stack
- AVEVA
- Wonderware
Implementation Scale
- Enterprise-wide Deployment
Impact Metrics
- Productivity Improvements
- Cost Savings
Technology Category
- Functional Applications - Enterprise Resource Planning Systems (ERP)
Applicable Industries
- Life Sciences
Applicable Functions
- Quality Assurance
- Discrete Manufacturing
Use Cases
- Manufacturing System Automation
- Predictive Maintenance
Services
- System Integration
- Software Design & Engineering Services
About The Customer
Fujirebio Diagnostics, Inc. is a global partner of choice among leading diagnostics companies around the world. With a reputation of more than 20 years as a trusted source of innovative solutions in clinical diagnostics, Fujirebio’s proven manufacturing process for the production of biomarkers has made it a global partner of choice among leading diagnostics companies around the world. Being in the life sciences industry, Fujirebio adheres to a strict manufacturing process which is based on Wonderware by AVEVA. These processes are certified with compliance for reporting and documentation requirements that are very detailed and extensive. The biomarkers produced by Fujirebio help physicians, lab professionals and patients better manage disease. Over the course of the year, Fujirebio’s 160,000- foot production facility produces about 75 million tests that are distributed throughout the world. It is a FDA-registered facility that is 21 CFR Part 11 compliant, and is both ISO 9001 and ISO 13485 certified for quality systems.
The Challenge
Fujirebio Diagnostics, a trusted source of innovative solutions in clinical diagnostics, was facing challenges with its existing paper-based GMP record system and manual process. The company was spending significant time each day manually reviewing reports. The paper-based system was not only time-consuming but also vulnerable to reporting errors. Moreover, any new system implemented had to enable the company to remain in compliance with federal regulation.
The Solution
Fujirebio implemented AVEVA's System Platform, Workflow Management, Historian, and InTouch HMI to replace its existing paper-based system. The solution, called the Electronic Initiative and the first phase of the implementation is called the Equipment Monitoring System (EMS), allows personnel to monitor equipment from their workstations, maintains all temperature readings in electronic records, notifies authorised personnel in the event of adverse temperature trends, generates electronic Good Manufacturing Practice (GMP) reports for review by exception, and provides authorised personnel electronic signature capabilities to approve reports. The EMS system at Fujirebio performs a number of very important functions. Workflow Management is at the heart of Fujirebio’s EMS. What Workflow Management does is digitise and automate Fujirebio’s manual processes that include people, equipment and systems, based on a sophisticated Business Process Management (BPM) foundation standard. This enables staff to generate electronic records and file them automatically.
Operational Impact
Quantitative Benefit
Case Study missing?
Start adding your own!
Register with your work email and create a new case study profile for your business.
Related Case Studies.
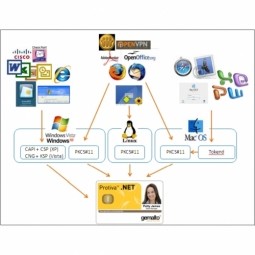
Case Study
Corporate Identity Solution Adds Convenience to Beckman Coulter
Beckman Coulter wanted to implement a single factor solution for physical and remote logical access to corporate network. Bechman Coulter's users were carrying smart card badges for doors, but also needed a one-time password token to access to our corporate network when they were not in the office. They wanted to simplify the process.
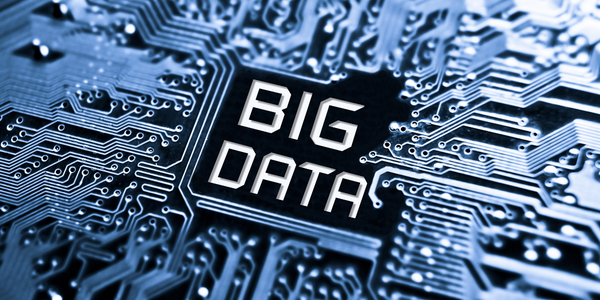
Case Study
Embracing Business Success in Real Time
· Increase control over growing Big Data to improve business decisions · Manage data for 28,000 biotechnology stockkeeping units in the fields of microbiology, molecular biology, animal cell cultures, plant tissue cultures, and lab ware for laboratory chemicals · Accelerate report generation and analysis with real-time data
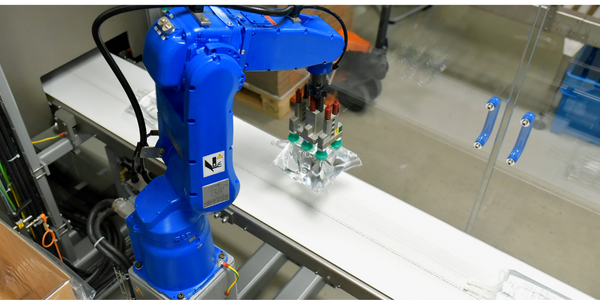
Case Study
Flow Robotics: Scaling Up Production and Accelerating Product Development with IoT
Flow Robotics, a Danish manufacturer, developed flowbot™ ONE pipetting robots to alleviate the strain on bioanalysts in life-science laboratories and hospitals across Europe. These robots were designed to automate part of the testing process, speeding up the time it takes to produce results and reducing pressure on staff. However, the company faced challenges in scaling up production and accelerating product development. High workloads and physically challenging conditions have long been an issue for laboratory professionals. Flow Robotics estimates that around half of medical lab technicians carry out the same arm movements for at least a quarter of their working day. The American Society for Clinical Pathology reported that 85% of laboratory professionals feel burnt out; 36% struggle with inadequate staffing; and 32% face a heavy workload and pressure to complete all testing on time.
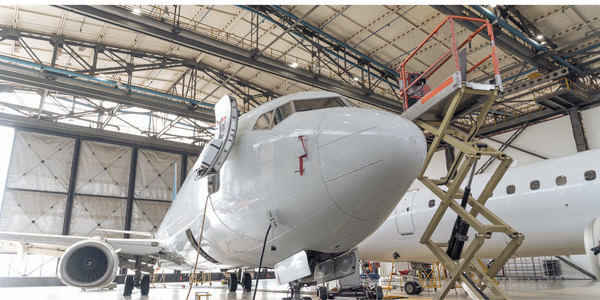
Case Study
Revolutionizing Aerospace Industry with 3D Printing: A 63% Lighter Titanium Part
GE Aviation, a renowned name in the aerospace industry, recognized the potential of 3D printing technology in transforming the sector. The primary challenge was to reduce the weight of the aerospace parts, which would directly impact the fuel costs. A lighter airplane would mean lower fuel consumption, leading to cost savings and a smaller carbon footprint. However, achieving this weight reduction without compromising the strength and functionality of the parts was a significant challenge. Traditional manufacturing methods were not able to provide the desired weight reduction while maintaining the required stiffness and strength of the parts. The challenge was to find a solution that could create strong, light, and functional aerospace parts.
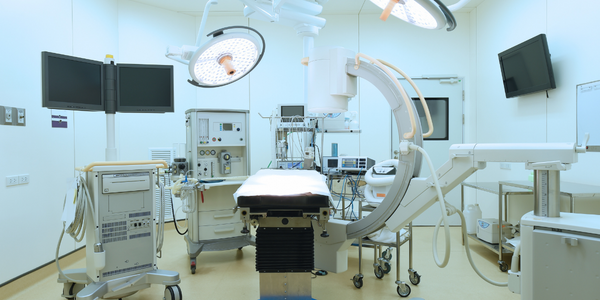
Case Study
Material Intelligence at Ethicon: Sustaining Medical Device Manufacturability and Improving Patient Care
Ethicon, a world-class medical devices company, faced several challenges in its operations. The rapid selection of manufacturing materials compliant in global markets was critical to assure patients, practitioners, and purchasing organizations of the biocompatibility of their medical devices. Ensuring supply chain continuity and minimizing risks of obsolescence for medical devices due to regulatory changes were also crucial in meeting Ethicon’s ongoing commitment to maintaining patient care. Furthermore, the engineers at Ethicon were developing the next generation of medical devices and needed to access historical material data to accelerate new product development. The process of centralizing and digitalizing its materials information was a significant challenge that Ethicon needed to overcome.
Case Study
IWT's Transformation: Customizing with Efficiency in IoT
IWT, a company specializing in the design, manufacture, and installation of washing systems for the life sciences and pharmaceutical industries, faced a significant challenge in managing its wide product portfolio. The company manufactures 45 different models, 60% of which are customized to some degree. This high level of customization, combined with limited production quantities, necessitated a controlled process for managing the release of engineering changes. The goal was to achieve efficiency, reduce process time, and better coordinate production throughout the organization. The need for strict compliance in heavily regulated industries further complicated the situation. IWT's existing PLM journey with Dassault Systèmes’ SOLIDWORKS for 3D CAD and Enovia for managing CAD data and Bills of Materials (BOMs) was proving inadequate. The system had limited part classification, no workflow, and no tool to ensure data consistency. The management of non-CAD documents was also a challenge, with information often difficult to find and access.