Technology Category
- Analytics & Modeling - Digital Twin / Simulation
- Infrastructure as a Service (IaaS) - Cloud Computing
Applicable Industries
- Cement
- Consumer Goods
Applicable Functions
- Product Research & Development
- Quality Assurance
Use Cases
- Experimentation Automation
- Virtual Prototyping & Product Testing
Services
- Hardware Design & Engineering Services
- Testing & Certification
About The Customer
Euro-Pro is a dynamic consumer products manufacturer that has been named one of the fastest growing private companies in the United States by Inc. Magazine for three consecutive years. The company's revenues tripled between 1997 and 2013, from less than $300m to over $900m. Euro-Pro boasts several household names in its product arsenal, including Ninja blenders and Shark vacuums. The company's engineering team is primarily located in China, while research and development (R&D) is conducted in the United States. The R&D team uses computer-aided engineering (CAE) tools and technologies to perform analysis and conduct tests in preparation for product launch.
The Challenge
Euro-Pro, a rapidly growing consumer products manufacturer, faced a challenge in its product development process. The company's product development was heavily reliant on physical prototype testing, which was time-consuming, costly, and often failed to provide a comprehensive understanding of product behavior during tests such as drops or impacts. The company wanted to increase the use of simulation to conduct more in-depth analysis of scenarios that were difficult or impossible to test physically, such as internal structural failures. The goal was to identify the root cause of product failures more accurately and provide better guidance to the engineering and product design teams. The company also aimed to test materials prior to their introduction on future generation products, with the hope of positively influencing the overall product portfolio direction in terms of market appeal, quality, reliability, and durability.
The Solution
Euro-Pro turned to Altair HyperWorks® for a solution. The company began using Altair solvers (OptiStruct, RADIOSS and AcuSolve) accessible via HPC cloud infrastructure for structural analysis and drop simulation. HyperMesh® was used to correct the geometry, saving around 50% time on meshing alone. Finite element analysis (FEA) provided more insight into impacts and cross-sections than was feasible with physical testing. RADIOSS® and AcuSolve® offered accurate and cost-efficient structural analysis and computational fluid dynamics (CFD) solutions respectively. The company used these tools to develop a finite element representation of vacuum cleaner sections and subjected them to various drop test and impact scenarios. This helped analysts better understand the root cause of potential problems, enabling them to rectify design issues without having to constantly build and test models at the point of failure reporting. The company accessed these solutions via HyperWorks On-Demand™, a high-performance computing (HPC) solution for design innovation in the cloud based on Altair’s patented usage-based license model.
Operational Impact
Quantitative Benefit
Case Study missing?
Start adding your own!
Register with your work email and create a new case study profile for your business.
Related Case Studies.
.png)
Case Study
Improving Vending Machine Profitability with the Internet of Things (IoT)
The vending industry is undergoing a sea change, taking advantage of new technologies to go beyond just delivering snacks to creating a new retail location. Intelligent vending machines can be found in many public locations as well as company facilities, selling different types of goods and services, including even computer accessories, gold bars, tickets, and office supplies. With increasing sophistication, they may also provide time- and location-based data pertaining to sales, inventory, and customer preferences. But at the end of the day, vending machine operators know greater profitability is driven by higher sales and lower operating costs.
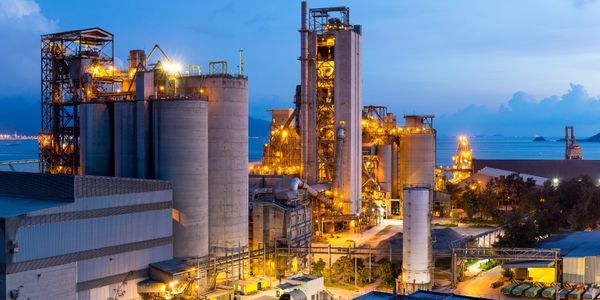
Case Study
System 800xA at Indian Cement Plants
Chettinad Cement recognized that further efficiencies could be achieved in its cement manufacturing process. It looked to investing in comprehensive operational and control technologies to manage and derive productivity and energy efficiency gains from the assets on Line 2, their second plant in India.
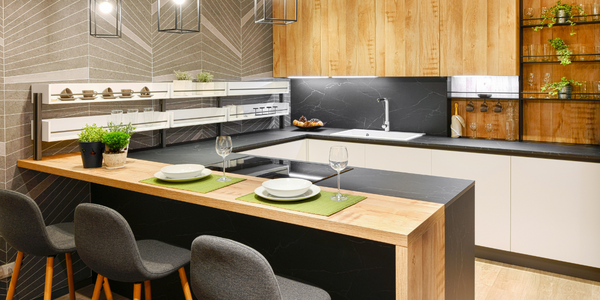
Case Study
Series Production with Lot-size-1 Flexibility
Nobilia manufactures customized fitted kitchens with a lot size of 1. They require maximum transparency of tracking design data and individual processing steps so that they can locate a particular piece of kitchen furniture in the sequence of processes.
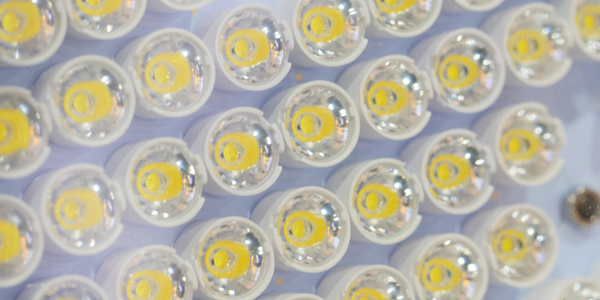
Case Study
American Eagle Achieves LEED with GE LED Lighting Fixtures
American Eagle Outfitters (AEO) was in the process of building a new distribution center. The AEO facility management team decided to look at alternate options for lighting layout that could provide energy and maintenance savings. AEO would need a full-time maintenance employee just to replace burned-out fluorescent tubes.