Technology Category
- Sensors - Autonomous Driving Sensors
- Sensors - GPS
Applicable Industries
- Buildings
- Transportation
Applicable Functions
- Facility Management
- Logistics & Transportation
Use Cases
- Last Mile Delivery
- Transportation Simulation
About The Customer
Corsicana Mattress Company is a leading mattress manufacturer in the United States. The company, which is celebrating its 50th anniversary, has grown from a family-owned business to one of the largest in the industry. Despite its rapid growth, the company faced challenges in maintaining efficiency, particularly in its logistics operations. The nature of its product made freight costly, and the company was exploring every possible option to reduce fixed and variable freight costs. However, it was limited by its analytical capabilities. The company was also grappling with the challenge of fulfilling orders from non-default facilities, which led to increased costs and inefficiencies.
The Challenge
Corsicana Mattress Company, one of the largest mattress manufacturers in the United States, was facing challenges in optimizing its shipping routes. The company, which had grown from a family-owned business, was grappling with inefficiencies in its logistics operations. The freight costs were high due to the nature of their product, and the logistics team was limited by their analytical capabilities. The company had instances of orders being fulfilled from non-default facilities, leading to increased costs and inefficiencies. In some cases, shipments were routed through facilities hundreds of miles away, leading to unnecessary costs and increased carbon emissions. The company lacked a system to audit default facility assignments, which was a manual and time-consuming process.
The Solution
The solution to Corsicana Mattress Company's challenge was developed in collaboration with the Logistics Director. The company leveraged Alteryx, a data analytics platform, to automate the process of auditing facility assignments. The first step involved geocoding the company's facilities and shipping locations and using the Find Nearest macro to generate a list of the closest facility for every shipping location. The company then compared this list with their existing default facility assignments, revealing thousands of incorrect assignments. The second phase involved narrowing the scope and defining the impact on capacity utilization at each facility. The company filtered out prospective default facility reassignments where the distance savings were relatively small. The analysis resulted in a list of potential default facility reassignments ranked by their savings potential. The company was also able to simulate the closure of a facility to identify the optimal way to reassign the locations serviced by the defunct plant.
Operational Impact
Quantitative Benefit
Case Study missing?
Start adding your own!
Register with your work email and create a new case study profile for your business.
Related Case Studies.
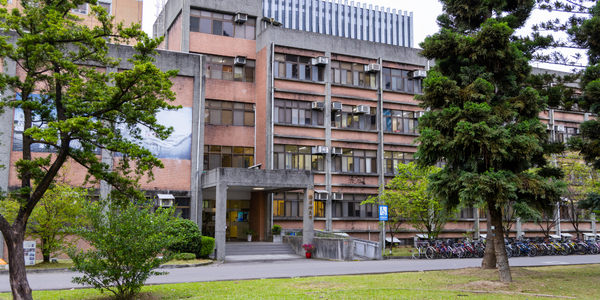
Case Study
Energy Saving & Power Monitoring System
Recently a university in Taiwan was experiencing dramatic power usage increases due to its growing number of campus buildings and students. Aiming to analyze their power consumption and increase their power efficiency across 52 buildings, the university wanted to build a power management system utilizing web-based hardware and software. With these goals in mind, they contacted Advantech to help them develop their system and provide them with the means to save energy in the years to come.
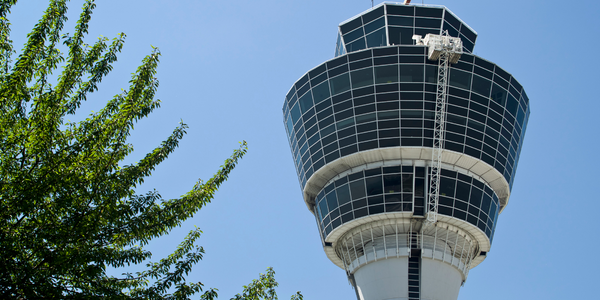
Case Study
Airport SCADA Systems Improve Service Levels
Modern airports are one of the busiest environments on Earth and rely on process automation equipment to ensure service operators achieve their KPIs. Increasingly airport SCADA systems are being used to control all aspects of the operation and associated facilities. This is because unplanned system downtime can cost dearly, both in terms of reduced revenues and the associated loss of customer satisfaction due to inevitable travel inconvenience and disruption.
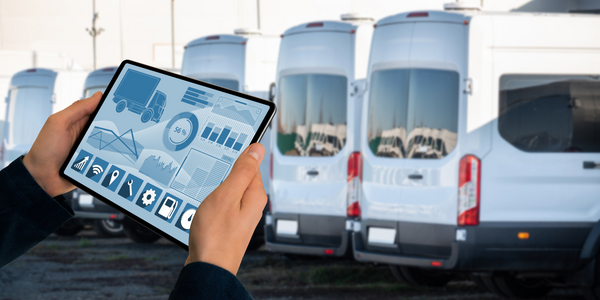
Case Study
IoT-based Fleet Intelligence Innovation
Speed to market is precious for DRVR, a rapidly growing start-up company. With a business model dependent on reliable mobile data, managers were spending their lives trying to negotiate data roaming deals with mobile network operators in different countries. And, even then, service quality was a constant concern.
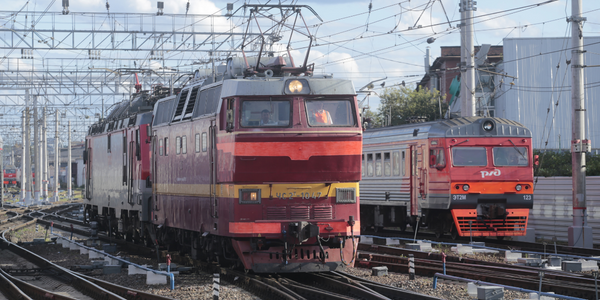
Case Study
Digitize Railway with Deutsche Bahn
To reduce maintenance costs and delay-causing failures for Deutsche Bahn. They need manual measurements by a position measurement system based on custom-made MEMS sensor clusters, which allow autonomous and continuous monitoring with wireless data transmission and long battery. They were looking for data pre-processing solution in the sensor and machine learning algorithms in the cloud so as to detect critical wear.
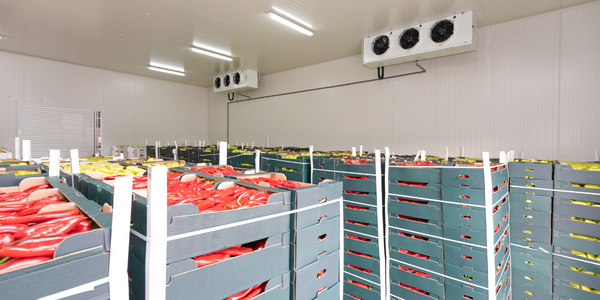
Case Study
Cold Chain Transportation and Refrigerated Fleet Management System
1) Create a digital connected transportation solution to retrofit cold chain trailers with real-time tracking and controls. 2) Prevent multi-million dollar losses due to theft or spoilage. 3) Deliver a digital chain-of-custody solution for door to door load monitoring and security. 4) Provide a trusted multi-fleet solution in a single application with granular data and access controls.
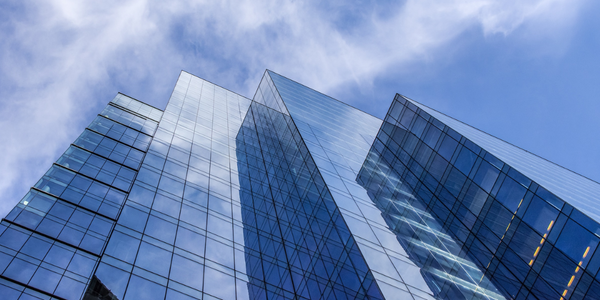
Case Study
Intelligent Building Automation System and Energy Saving Solution
One of the most difficult problems facing the world is conserving energy in buildings. However, it is not easy to have a cost-effective solution to reduce energy usage in a building. One solution for saving energy is to implement an intelligent building automation system (BAS) which can be controlled according to its schedule. In Indonesia a large university with a five floor building and 22 classrooms wanted to save the amount of energy being used.