AVEVA helps a well-established Canadian shipyard stay competitive in the field, and increase efficiency and meet deadlines easily.
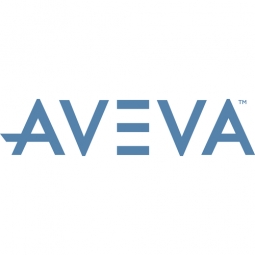
Customer Company Size
Large Corporate
Region
- America
Country
- Canada
Product
- AVEVA ERM
- AVEVA Marine
- AVEVA Global
Tech Stack
- SAP
Implementation Scale
- Enterprise-wide Deployment
Impact Metrics
- Productivity Improvements
- Cost Savings
Technology Category
- Platform as a Service (PaaS) - Connectivity Platforms
Applicable Industries
- Marine & Shipping
Applicable Functions
- Discrete Manufacturing
- Procurement
Use Cases
- Supply Chain Visibility
- Process Control & Optimization
Services
- System Integration
About The Customer
Established in 1825, Chantier Davie shipyard is Canada’s oldest and largest shipbuilder, and one of the country’s leading and most innovative shipyards. Situated in Quebec, the yard has been continuously expanding in both working and production capacity, and its 1,300 workers now have the capability to handle 1,200 t/month of steel production, at their 570,000 m2 facilities. Davie provides value-added, specialised products and services, making full use of its high-capacity fabrication capabilities to provide complex engineered solutions to meet its clients’ needs. The company’s ability to provide end-to-end turnkey solutions, combined with its strategic location, makes Davie the partner of choice for clients across a broad range of industries from offshore oil & gas to defence.
The Challenge
Chantier Davie (Davie), a diversified shipbuilder, produces various types of ships for both naval and commercial clients. The latest project, called ‘Resolve’, is the conversion of a 182.5-metre container ship into an auxiliary oil replenishment vessel for the Canadian Navy, to be completed in only 24 months, including design and delivery. To achieve the deadline for the complex rebuild, Davie had to evaluate existing tools and processes, to maximise efficiency across design, planning, supply chain and production. Before engaging with AVEVA ERM, Davie was facing several challenges in the planning and supply-chain domains. The challenges revolved around missing visibility of materials for planning, and around planning for the supply chain. Most of the systems used for supply chain and planning management were home-grown and supplemented with various Microsoft Excel sheets and Access databases.
The Solution
The transformation process was initially started with the introduction of AVEVA ERM and AVEVA Marine, and also AVEVA Global, a tool which allows teams from multiple locations to work on the same model. This allowed Davie to optimise their concurrent design processes together with multiple European design agencies. Davie started its transition by purchasing SAP for financials and, shortly thereafter, AVEVA ERM for material management and planning. One of the challenges which has been overcome is that of missing materials on the shop floor, where Davie, thanks to AVEVA ERM’s integrated planning and materials management capabilities, can now see the status/ availability of materials before releasing jobs for production.
Operational Impact
Case Study missing?
Start adding your own!
Register with your work email and create a new case study profile for your business.
Related Case Studies.
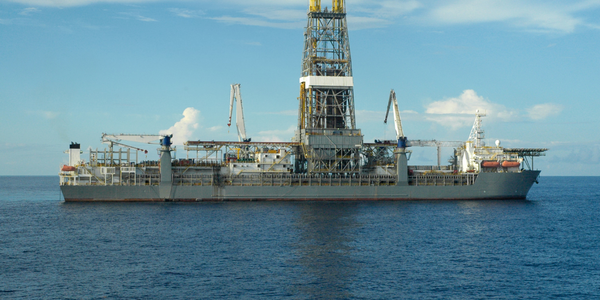
Case Study
Drill ship power challenge: hybrid solution solves distribution issues
Aspin Kemp & Associates (AKA), a manufacturer of electrical power and control systems headquartered in Montague, PEI, encountered one with its hybrid power initiative, the first hybrid drill floor destined for installation on ultra-deepwater drill ships operated by Transocean, Swiss offshore drilling contractors. Since on-site modification was impossible and scrap recycling of any modifications was unacceptable, the enclosures had to arrive ready-to-install.

Case Study
Ensures Tanker Safety and Emissions Compliance
Storage tanks are irregular in shape and a certain amount of mathematical modelling is required to get an accurate representation of volume and, more importantly, the weight of material in each tank. In addition, countries have different emission regulations, so the ships position needed to be accurately known in order to geotag emission data.
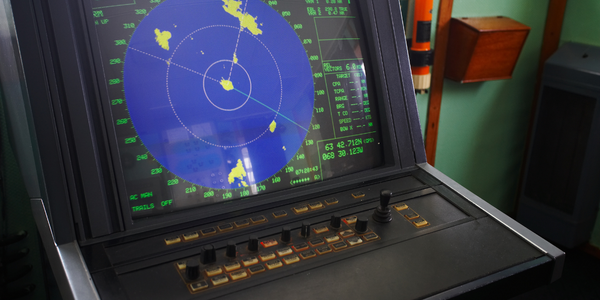
Case Study
Real-time Networked Sonar System for Ships
A multinational, knowledge-based corporation that delivers marine electronics solutions is utilizing industrial Ethernet technology to help ensure that operations at sea are dependable and optimal. Based in Europe, the company has nearly 4000 employees working in 20 countries around the world, and produces high-tech systems for offshore oil and gas operations, merchant marine systems, and various applications for the defense and aerospace industries. The company produces products and systems used by merchant vessels and offshore installations for positioning, navigation, automation, as well as for surveying and monitoring the seabed, and for fishing vessels and fi sheries research. As one of the major suppliers of high quality marine electronics in the world, their products include chart plotters for yachts, triple redundant dynamic positioning systems for oil drilling rigs, and sonar and instrument systems for scientifi c research vessels. Products used for marine applications must be rugged enough to endure the corrosive effects of salt water, and be able to withstand excessive amounts of vibration and shock. For this reason, the company only uses DNV and GL certified products and components to ensure that their systems can meet the high standards required by the maritime industry.
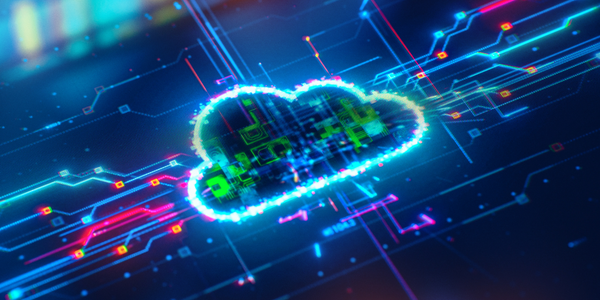
Case Study
Fleet Management Connectivity Solution for Marzam
Marzam, in order to ensure the best service, invested 3 million dollars in the construction of 2 fuel oil tanks with 40k gallons and 10k gallons capacity each, located in Manta, Ecuador. The customer needs to keep fleet operations going with fuel available at all times in order to guarantee quality of service. KEY ELEMENTS FOR THE CUSTOMER: Real-time level monitoring: Tank infrastructure remote level monitoring. Configure alerts and notifications when reaching critical values to avoid the need for emergency refills and optimize supply schedules. Real-time consumption monitoring: The customer needed an easy way to monitor in real-time accurate values of consumption.
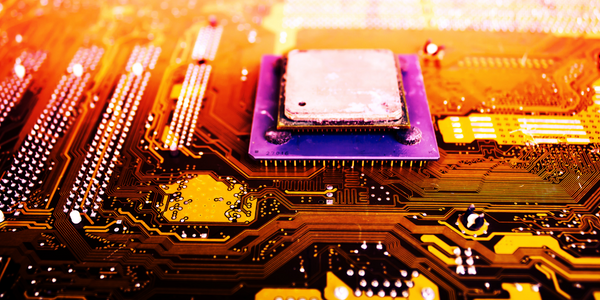
Case Study
Mitsubishi Electric's Edge Computing Solution Powered by Wind River VxWorks
Mitsubishi Electric Corporation, a global leader in factory automation (FA) applications, identified edge computing as a critical component of the Industrial Internet of Things (IIoT). The company aimed to enhance device and data security, reduce data traffic to the cloud, and enable faster response to network or device issues. In 2018, Mitsubishi Electric launched its first line of industrial hardware products designed for edge computing, the MELIPC Series. The primary development goals for MELIPC were to support the type of edge computing promoted by Mitsubishi Electric and to introduce advanced vision technology for device control. The flagship computer of the MELIPC line, the MI5000, was designed to combine real-time equipment control with high-speed data collection, processing, diagnosis, and feedback in a single machine. However, the development team needed a real-time control platform that could seamlessly integrate real-time control with proven analytic and diagnostic applications.
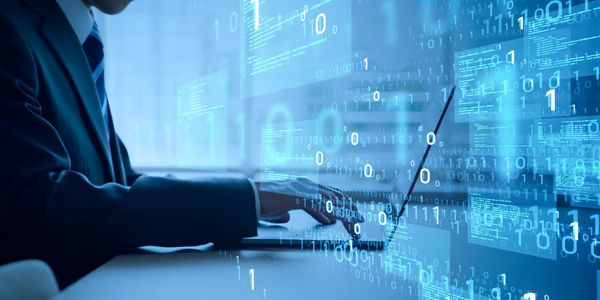
Case Study
Migrating to Software-Only Licenses for More Responsive License Management
The world’s premier shipping companies work with the software solutions of ABB Marine & Ports to get their vessels safely and efficiently to their destinations. A loyal customer of Wibu-Systems for over a decade, ABB has been relying on CodeMeter dongles to store the license keys for their ABB AbilityTM Marine Advisory System - OCTOPUS.The current version of the system is using Wibu-Systems’ robust metal-case CmStick ME, a perfect choice for the rugged conditions at sea. As satellite communications has made fast Internet connections at sea a common reality for maritime operators, the company is looking to move from physical to software solutions to streamline its logistics processes.