Technology Category
- Analytics & Modeling - Digital Twin / Simulation
- Infrastructure as a Service (IaaS) - Virtual Private Cloud
Applicable Industries
- Packaging
- Plastics
Applicable Functions
- Procurement
- Product Research & Development
Use Cases
- Intelligent Packaging
- Manufacturing Process Simulation
Services
- Testing & Certification
- Training
About The Customer
Amcor Rigid Plastics is a leading product supplier for food, beverage, healthcare, personal and homecare packaging segments. The company is headquartered in Ann Arbor, Michigan with over 59 manufacturing plants in 13 counties and over 6,000 employees. Working within the rigid plastics industry, the demand for sustainable practices are high. The company is continually looking for innovative and lightweight container designs which would be aesthetically pleasant and have an ease in handling for the consumer without compromising the quality, performance or safety. Simulation plays a major role in ensuring Amcor’s lightweight packages meet the functionality requirements.
The Challenge
Amcor Rigid Plastics, a leading product supplier for various packaging segments, was facing challenges in maintaining a balance between packaging performance, environmental impact, and shelf appeal while keeping costs to a minimum. The company was under pressure to create more environmentally friendly products. Amcor was also looking for innovative and lightweight container designs that would be aesthetically pleasing and easy to handle for the consumer without compromising on quality, performance, or safety. The company was using Altair’s HyperWorks suite to create accurate finite element models of the concept designs from the CAD teams to assess their performance in the virtual world. However, they wanted to explore ways to accelerate the engineering and analysis tasks associated with the development of new packaging products. The virtual test process used to investigate the performance of new packaging designs under various loading and impact scenarios was consuming a large amount of the simulation team’s time.
The Solution
Altair ProductDesign’s Enterprise Solution Group (ESG) worked with Amcor’s simulation specialists to identify where time and costs could be saved within the design process. They suggested that Amcor could take advantage of the Impact Simulation Director (ISD), which automates the laborious, manual tasks associated with model setup, analysis, postprocessing, and reporting. Altair ProductDesign worked closely with Amcor’s team to understand the existing impact simulation process in order to identify how the ISD could be best implemented to avoid disruption to the ongoing product development cycle. On-site training sessions were organized to help achieve a quick and effective adoption of the solution. Once implemented, the ISD was able to accelerate the modeling process by allowing the user to define mesh criteria for each part, automatically mesh the model and then quickly check mesh quality and status. The solution guides the analyst through the impact simulation process, creating solver decks from CAD geometry for a wide variety of analyses.
Operational Impact
Quantitative Benefit
Case Study missing?
Start adding your own!
Register with your work email and create a new case study profile for your business.
Related Case Studies.
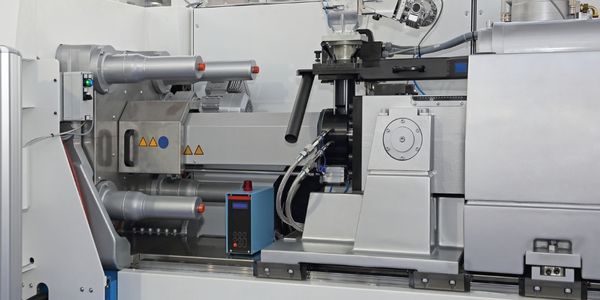
Case Study
Plastic Spoons Case study: Injection Moulding
In order to meet customer expectations by supplying a wide variety of packaging units, from 36 to 1000 spoons per package, a new production and packaging line needed to be built. DeSter wanted to achieve higher production capacity, lower cycle time and a high degree of operator friendliness with this new production line.
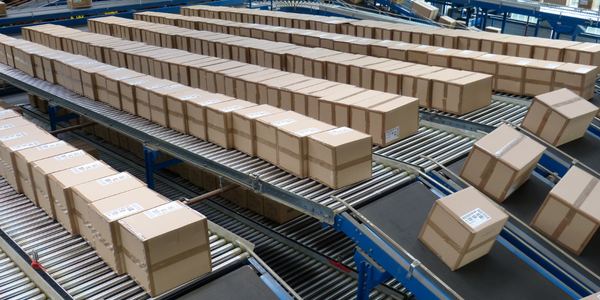
Case Study
IoT Data Analytics Case Study - Packaging Films Manufacturer
The company manufactures packaging films on made to order or configure to order basis. Every order has a different set of requirements from the product characteristics perspective and hence requires machine’s settings to be adjusted accordingly. If the film quality does not meet the required standards, the degraded quality impacts customer delivery causes customer dissatisfaction and results in lower margins. The biggest challenge was to identify the real root cause and devise a remedy for that.
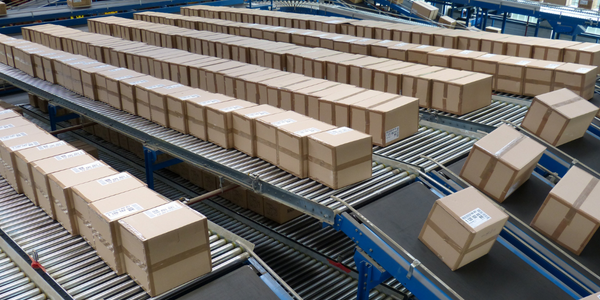
Case Study
Zenon the Ideal Basis for An Ergonomic HMI
KHS develops and produces machines and equipment for filling and packaging in the drinks industry. Because drinks manufacturing, filling and packaging consist of a number of highly complex processes, the user-friendly and intuitive operation of equipment is increasingly gaining in significance. In order to design these processes as simple as possible for the user, KHS decided to introduce a uniform, transparent and standardized solution to the company. The HMI interface should meet the requirement for people with different qualifications and enable them to work on a standard platform.
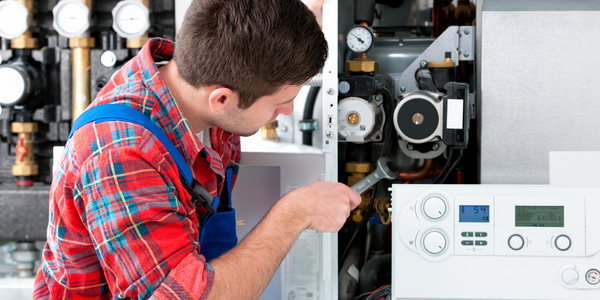
Case Study
Boiler Control System for Plastic Manufacturing Applications
Factory automation applications must be equipped to handle and monitor the myriads of information from attached devices. For plastic manufacturing applications, the boiler control system plays a critical role by gathering and regulating information to ensure production is accurate and smooth. In this particular case, the customer combines eight subsystems that include power meters, water meters, alarm output, displays, and I/O status to be controlled by several intelligent controllers with Modbus RTU interface. The Modbus TCP protocol is used for this application due to the distance. System Requirements: • Modbus serial to Modbus TCP translation • Multiple slaves/masters support • Automatic Modbus TCP response time detection
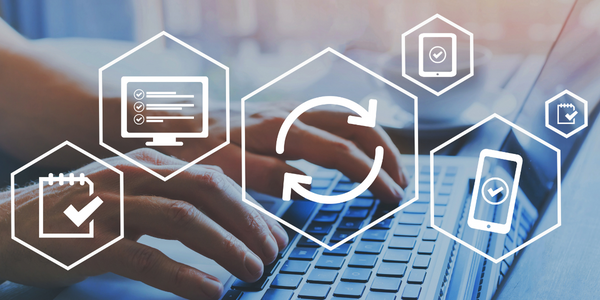
Case Study
Ascend Performance Materials Case Study
Ascend operations must access multiple software systems to manage day-to-day operations in an effective and secure manner. These systems generate large sets of data which contain critical information pertaining to management systems, planning and cost information in business systems and energy consumption. As a result, Ascend management was challenged with creating relevant reports reflecting performance measures in overall context of their operational process. The company’s previous process entailed collecting and analyzing data manually which was not effective, since the information collected was generated after the fact, and was too complex for collaborative use across the organization.
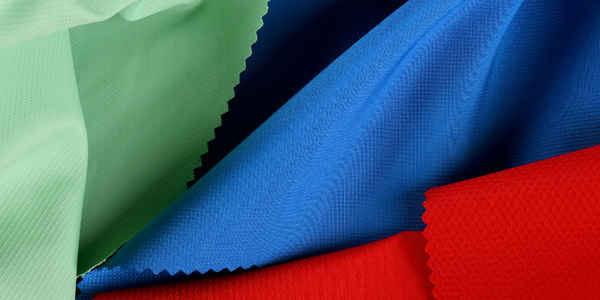
Case Study
Remake Enterprise-to-production System
The client was running a legacy material flow tracking system and wanted to replace the system with a more effective one as the system was increasingly expensive to maintain and support and also was not extendable. The client's IT landscape was filled with modern applications and it was difficult to interface the material flow tracking system with modern applications.